Use of Foam for FireFighting in Tank Farms of the Oil and Petrochemical Industry
Tank farm fires in the oil and petrochemical industry do not occur often. When they do occur, it is with devastating consequences and negative publicity. This article will describe the typical incident scenarios and present foam as the most suitable extinguishing agent together with the firefighting equipment most commonly used. Finally, it is questioned whether the lessons learned from every incident are being taken into consideration.
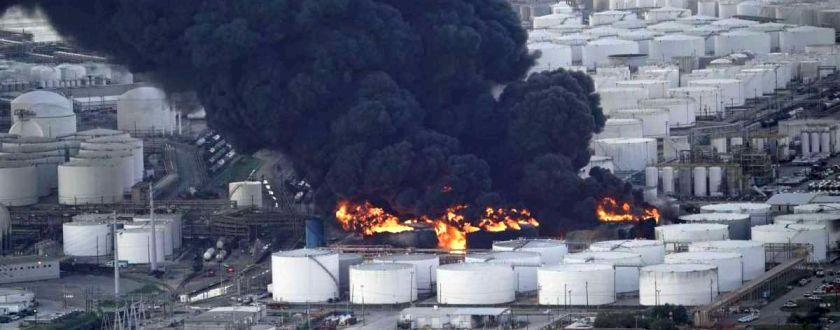
Tank farm fire at Deer Park, Texas, USA
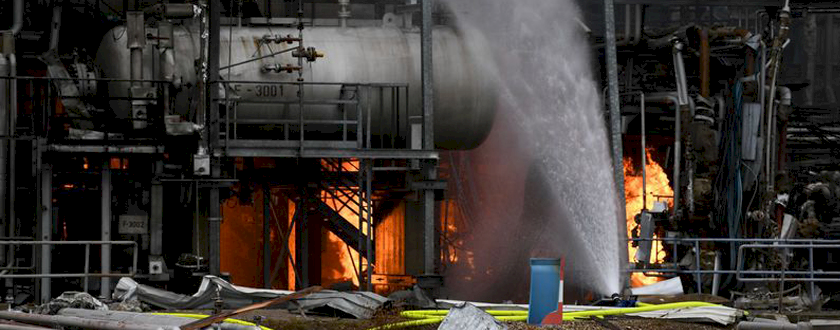
Devastation after explosion and fire in a petrochemical plant
Most recently, a number of fires caused massive damage to tank farms, oil refineries and loading terminals. Prominent examples include the ITC tank farm at Deer Park, Texas, USA in March 2019 and the refinery fire at Baton Rouge, Louisiana, USA in February 2020.
Sadly, only news of this kind makes its way into the news, unlike near-miss accidents where improved fire protection technology has prevented worse outcomes. This means that both fire protection and extinguishing methods must be improved to minimize the effects of future fires. Fire protection systems in hazardous areas of the oil and gas industry (fire class B) require unique extinguishing systems as foam is considered the best extinguishing agent for liquid fires. The use of water can be important as well; however, for cooling the tank wall and adjacent tanks.
Luckily, such large-scale incidents do not happen frequently; but when they do, they may have a severe impact on humans, local eco-systems and the general environment. Extinguishing full-surface oil tank fires is very challenging and the rate of success is low. Many authorities and companies have not learned from such incidents, some of which can be disastrous.
Common tank farm configurations
The tanks in use are typically classified by roof type and diameter. They are distinguished between fixed roof, floating roof and fixed roof tanks with a floating cover. Flammable liquids are commonly stored in tanks with a floating cover or roof; explosive fluids, in turn, are stored in tanks with a fixed roof. The tank diameters are normally between 20m and 80m, although larger tanks up to 120m tanks are also used. Their heights usually vary between 10m and 25m. This article is focusing on firefighting techniques and will not deal with tank types in more detail.
Laws and regulations
Diverse regional and national laws exist worldwide concerning fire protection. This article will be addressing the basics of the globally applied NFPA11 issued by the National Fire Protection Association, the standard for firefighting foam.
In place of various national and international certifying bodies, the following should be mentioned: the VdS approval in Germany (Verband der Sachversicherer translated to Association of Property Insurers) and the FM approval (Factory Mutual) on an international stage. Specifically, VdS and FM have prepared particular testing procedures for firefighting systems and have the necessary facilities and specialist personnel for testing.
Typical incidents
Fire incidents in tank farms of the oil and petrochemical industry occur in different scenarios, with consequences ranging from minor to disastrous. The most typical scenarios are listed as the following:
-
Rim Seal Fire
Rim seal fires occur on tanks with a floating cover. They can be extinguished quickly by the use of stationary systems as long as they are detected early enough. A longer fire, however, may damage the seal and, hence, cause an excess release of oil. This may develop into an extensive fire. A seal failure releasing excess fluid, or excessive use of extinguishing fluid, may lead to sinking of the floating cover and eventually to a full surface fire.
-
Vapor ignition
When storing petrochemical fluids, vapors may leak and be ignited by external sources, such as a lightning strike.
-
Dyke area fires
Tank farms are normally safeguarded by a dyke or located inside a basin to contain any escaping liquids. If oil or petrochemical fluids leak from a tank unintendedly, they may catch fire. If the fire is detected early enough, such fires can normally be extinguished easily and quickly by the use of fixed or mobile extinguishing equipment. If this is not the case, it can lead to a large surface fire which can also spread on the tank.
-
Explosion
Transformation of explosive gases by an ignition source. This normally causes damage to stationary extinguishing systems and mobile systems must be used. In addition, an explosion usually results in spreading the flammable liquids and devastation of the adjacent areas and access roads.
-
Boilover
A boilover may happen in case of a long-lasting oil tank fire where water has gathered at the bottom of the tanks. Due to the oil heating up to several hundred degrees Centigrade, the water may evaporate abruptly. The water steam rises to the surface in bubbles which burst at the surface and spread the oil above the tank. The enlarged surface area causes an abrupt fireball.
-
Full-surface tank fire
If oil or petrochemical liquids escape, they gather on the floating roof. In the worst case, even a sinking of the floating roof can occur. If this surface catches fire, a full-surface tank fire develops rapidly. Fires on tanks with a floating roof can be extinguished either by stationary extinguishing systems from inside or by mobile extinguishing systems from outside the dyke area. In the case of fixed-roof tanks, only the internal stationary extinguishing systems can be used until the roof collapses.
Foam as an extinguishing agent
Foam has proven to be the best medium to extinguish fluid fires. Foam consists of the components; water, foam concentrate and air. The foam concentrate is mixed with the extinguishing water at a precisely defined rate. Air is then added to this premix to generate the foam. Depending on the foam concentrate and the quantity of air, different types of foam are produced to extinguish different types of fire. Foam forms a homogenous layer of air bubbles, increasing the extinguishing agent's volume and, hence, reducing its density. The foam floats on top of the flammable liquid and spreads across its surface. Due to this and its chemical properties, the foam blanket suppresses the release of flammable vapors, cuts off the supply of air and cools down the substance on fire. Consequent application of foam until fully covering the entire surface of the burning liquid will finally smother the fire.
Foam concentrates are developed for specific proportioning rates. The most common ones are 1% and 3%. As a general rule, a foam concentrate can form a stable and functioning foam only if it is mixed to the extinguishing water at no less than the correct proportioning rate. An increased proportioning rate will still form a stable and functioning foam; however, the foam concentrate stored will be used up faster. A proportioning rate falling short will produce a foam which is unable to develop its full extinguishing power.
Request a quote
You are interested in our proportioners? We will be happy to help you along. Request a non-binding quotation from us!
Stay informed
The FireDos newsletter always keeps you well-informed. Stay up-to-date on all aspects of fire extinguishing technology.
The foam concentrates are divided into three groups:
-
Protein foam concentrates
Most prominently, there are film-forming fluoro-protein foam concentrates and film-forming alcohol-resistant* fluoro-protein foamconcentartes.
-
Synthetic foam concentrates
The most important ones are film-forming and film-forming alcohol-resistant* foam concentrates. The majority of existing synthetic foam concentrates contain fluorine which has good extinguishing properties.
-
Fluorine-free foam concentrates
Mainly due to environmental reasons, fluorine-free synthetic foam concentrates, as the third group, have and are are being developed. Fluorine-free foam concentrates have yet to be fully proven for all foreseeable fire scenarios as suitable replacements for existing fluorine based foam concentrates. In addition, due to their different physical properties (all existing fluorine-free foam concentrates have an increased viscosity and pseudoplasticity compared to the fluorine-containing foam concentrates), the necessary proportioning equipment has to be checked for its suitability.
After synthetic foam concentrates were introduced in the 1970s, various testing was conducted. One testing series by Shell in 1982 revealed that fires could be extinguished within 2 to 4 minutes if a good and suitable foam concentrate was used, both protein and synthetic. The extinguishing attempts were carried out in an open tank where the oil was on fire for 30 minutes and the surface temperature was about 800 - 900 °C. Basically, the conditions for these low extinguishing times were as follows:- suitable foam concentrate
- sufficient foam concentrate supply
- sufficient water supply
- functioning extinguishing equipment in sufficient quantity (well-maintained, quick and easy access, correct strategic placement)
- trained personnel
- quick implementation of a suitable plan of action
*Alcohols are water-miscible, which would destroy the foam. In alcohol-resistant foam concentrates, this is prevented by forming a polymer layer
Steps of foam generation

Extinguishing systems
Depending on the tank type and the size of the tank farm, the extinguishing systems must be designed differently. A fixed-roof tank must have a fixed extinguishing system which allows discharging foam under the roof. An application from mobile systems outside is possible only if the roof has been damaged or removed by a fire or an explosion. In case of a floating-roof tank, the foam can be applied by use of fixed or mobile systems from outside.
Fixed extinguishing systems typically consist of one or more stationary fire pumps, one proportioner and tank for the foam concentrate, discharge devices such as foam nozzles, sprinklers, foam pipes or fire monitors and the corresponding piping.
Mobile systems generally consist of the same components (fire pump, proportioner, supply tank); these must, however, be available in mobile form on vehicles or trailers. In addition, only fire monitors are usually used as discharge devices. The piping/lines consist of hoses and suction pipes. Beside the tactical positioning of the foam discharge points, including mobile units, the foam concentrate and its proportioning into the extinguishing water are the most important factors for successful extinguishing. This will be looked at more closely referring to NFPA 11.
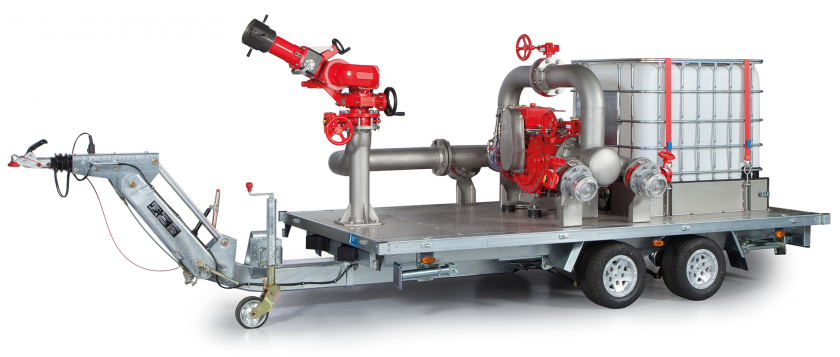
Trailer with M4 monitor
Foam concentrate
When storing the foam concentrate in suitable containers, attention must be paid that they are stored a sufficient distance away from the objects to be protected. The quantity must be sufficient to allow extinguishing of the largest protected object, or of the objects to be protected simultaneously as a minimum. The proportioning rate (1% or 3%) will dictate the quantity of the foam concentrate required. Generally, it is important not to mix different foam concentrates or foam concentrates with different proportioning rates as this can lead to unstable foam formation. Below is an example calculation for the foam demand according to NFPA 11.
Tank surface x specific extinguishing water quantity x proportioning rate of foam concentrate x requested minimum extinguishing time
In case of a crude oil tank with 60m diameter, NFPA 11 requires an application of 6.5l/(min*m2) for an extinguishing time of 65 min.
- When using a 3% foam concentrate, this results in a minimum amount of approx. 36 000 liters of foam concentrate and a required extinguishing water flow rate of approx. 18 000 l/min. NFPA 11 recommends stocking additional foam concentrate for the dyke area of about the same amount. In addition, a safety factor of 2 is recommended to compensate foam losses during extinguishing caused by, e.g., wind and other factors. This results in a stock of 144 000 l of 3% foam concentrate.
- If alternatively a 1% foam concentrate is used the total storage quantity would amount to only 48 000 l requiring smaller storage tanks and set up space.
- The choice of foam concentrate and proportioning rate is dictated by the fluid to be extinguished.
Foam concentrate proportioning
NFPA 11 describes various types of foam concentrate proportioning equipment. In the following, three systems are looked at which are most common. Tight limits for the proportioning of foam concentrate apply to all of them.
The proportioning rate must not be less than the permitted values – i.e. 3% for a 3% foam concentrate or 6% for a 6% foam concentrare.
The proportioning rate must not exceed 30% above the permitted value i.e. 3.9% for a 3% foam concentrate or 7.8% for a 6% foam concentrate; respectively, the proportioning rate is allowed to be an absolute maximum of 1% above the permitted value – i.e. 4% for a 3% foam concentrate or 7%
for a 6% foam concentrate (the smaller value must be used respectively).
To guarantee correct proportioning, the proportioner, including the proportioning rate must be tested at least once per year and its correct functioning must be checked.
Bladder tank with proportioner
The bladder tank with a proportioner is a proven and cost-effective technology. The bladder tank is a pressurized vessel with a bladder inside which is filled with foam concentrate. The tank is pressurized with water from the fire extinguishing line and discharges the foam concentrate from the bladder as required. The bladder is connected to a proportioner which operates using the venturi principle. When the fire pumps are activated, pressure is generated by the pump, causing delivery of foam concentrate to the proportioner. The extinguishing water flows through the venturi proportioner. The resulting vacuum induces the foam concentrate into the extinguishing water flow. The advantages of this system are its simple design without moving parts and its easy operation. No external energy is required and the system is relatively inexpensive.
A disadvantage is that the system is a pressurized vessel subject to corresponding regulations such as ASME Boiler & Pressure Vessel Codes. In order to refill foam concentrate, the system must be shut down and drained. The rubber bladder is sensitive; when damaged, water will contaminate the foam concentrate. At a given proportioning rate, the system is only suitable for low variations in the extinguishing water flow pressure and volume. Adding or changing individual foam discharge devices is possible only to a very limited extent. The system is also unsuitable for proportioning highly viscous foam concentrates.
To conduct any mandatory required annual testing, the system must be activated and premix generated at the venturi proportioner within in the extinguishing water line. The correct proportioning rate must be measured in the premix by laboratory analysis. The generated premix must be disposed of. The consumed foam concentrate in the bladder tank needs to be replaced.
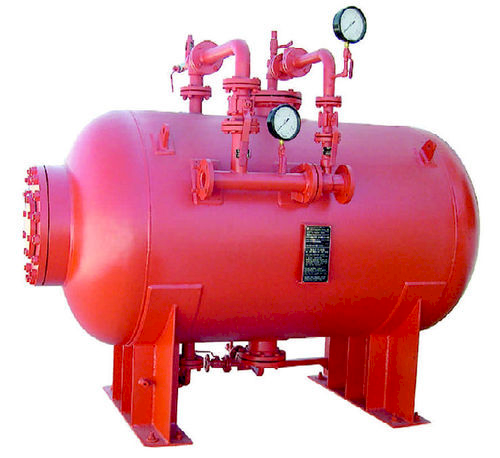
Bladder tank with proportioner
Driven proportioning pump with flow meter
The system consists of an atmospheric tank for the foam concentrate, an electric or diesel-powered foam concentrate pump with an electronically controlled valve and a flow meter in the extinguishing water flow line. When the fire pumps are activated, the foam concentrate pump drive and electronic control system must be activated. The extinguishing water flow rate is measured by the flow meter and the control system adjusts the correct foam concentrate quantity via the control valve. The foam concentrate is injected into the extinguishing water flow by the foam concentrate pump. If there is a change in the flow rate, the amount of injected foam concentrate is regulated by the control valve.
The system's advantage lies in the precise proportioning of the foam concentrate, independent of the extinguishing water pressure or flow rate. Foam concentrate can be topped up during the extinguishing operation. The system is capable of proportioning highly viscous foam concentrates. For the purpose of annual testing, the system must be activated; however, the delivered foam concentrate can be measured via a return line.The proportioning rate is calculated from the extinguishing water / foam concentrate flow rate. No premix is produced; and as the foam concentrate is passed back into the tank, no foam concentrate needs to be refilled.
Disadvantages are the requirement for an external interruption-free energy supply for the foam concentrate pump and the control system, as well as the need for a sophisticated control system and the comparatively higher purchasing costs. Furthermore, it must be accepted that a delay occurs between the change of the extinguishing water flow rate and the newly adjusted foam concentrate amount. The foam quality may be compromised when constantly changing operating conditions as foam discharge devices are turned on or off or changed.
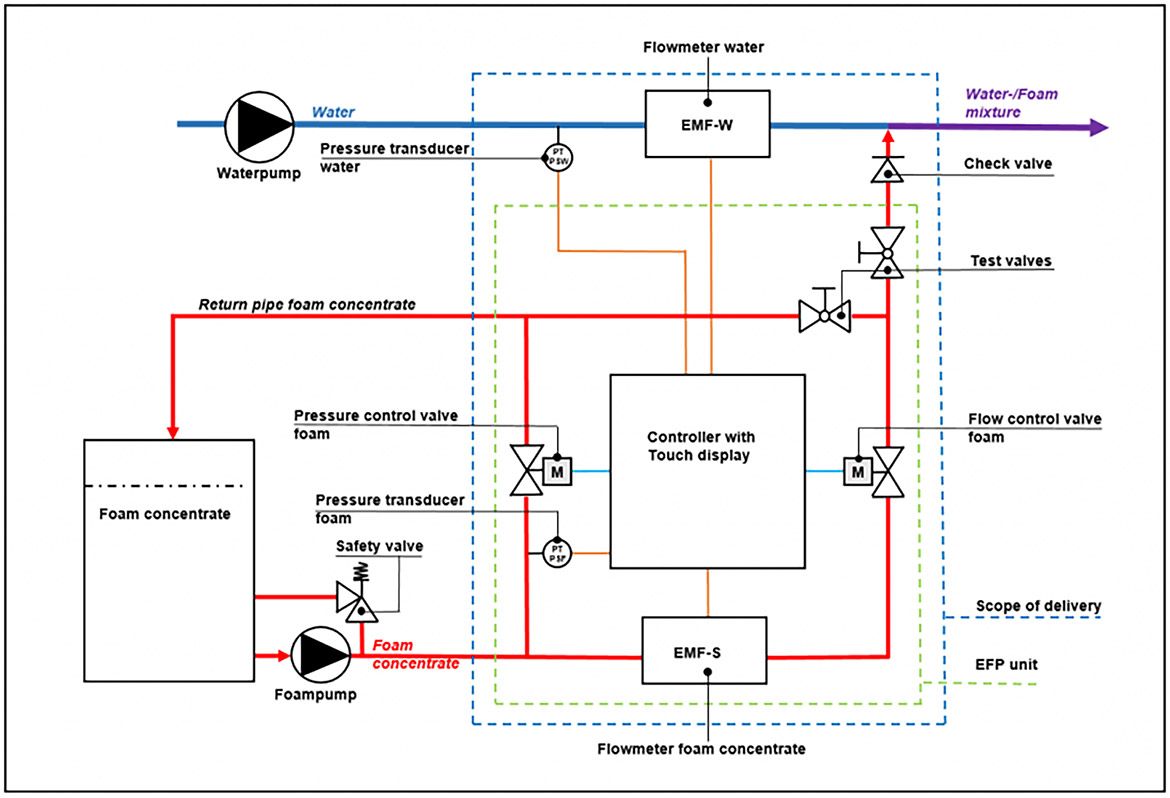
Driven proportioning pump with flow meter
Water motor with proportioning pump
The system consists of an atmospheric tank for the foam concentrate, a water motor installed in the extinguishing water flow line and a foam concentrate pump which is connected directly to the water motor. Water motor and pump form one compact unit. Upon activation of the fire pumps, rotation in the water motor starts. The direct coupling to the foam concentrate pump affects immediate foam concentrate injection into the extinguishing water. If the flow rate changes, the amount of foam concentrate is adapted immediately.
The advantage of the system is its independence from external energy sources as well as a precise and immediate foam concentrate proportioning regardless of the extinguishing water pressure or flow rate. If a piston or plunger pump is used, adjustment or calibration after installation is not necessary since the water motor and the pump are volumetric devices firmly connected to each other. Foam concentrate refilling during operation is possible. The system is also capable of proportioning highly viscous foam concentrates. The system must be activated for annual testing; however, the delivered foam concentrate can be measured via a return line. The proportioning rate is calculated from the extinguishing water / foam concentrate flow rate. No premix is generated; and if the foam concentrate is passed back into the tank, no foam concentrate needs to be topped up. The larger design and the comparatively higher purchasing costs are a disadvantage of the system.
With any system, consideration should be taken into account for the annual testing costs, which can be considerable in terms of replacement foam concentrate, disposal of premix and manpower.
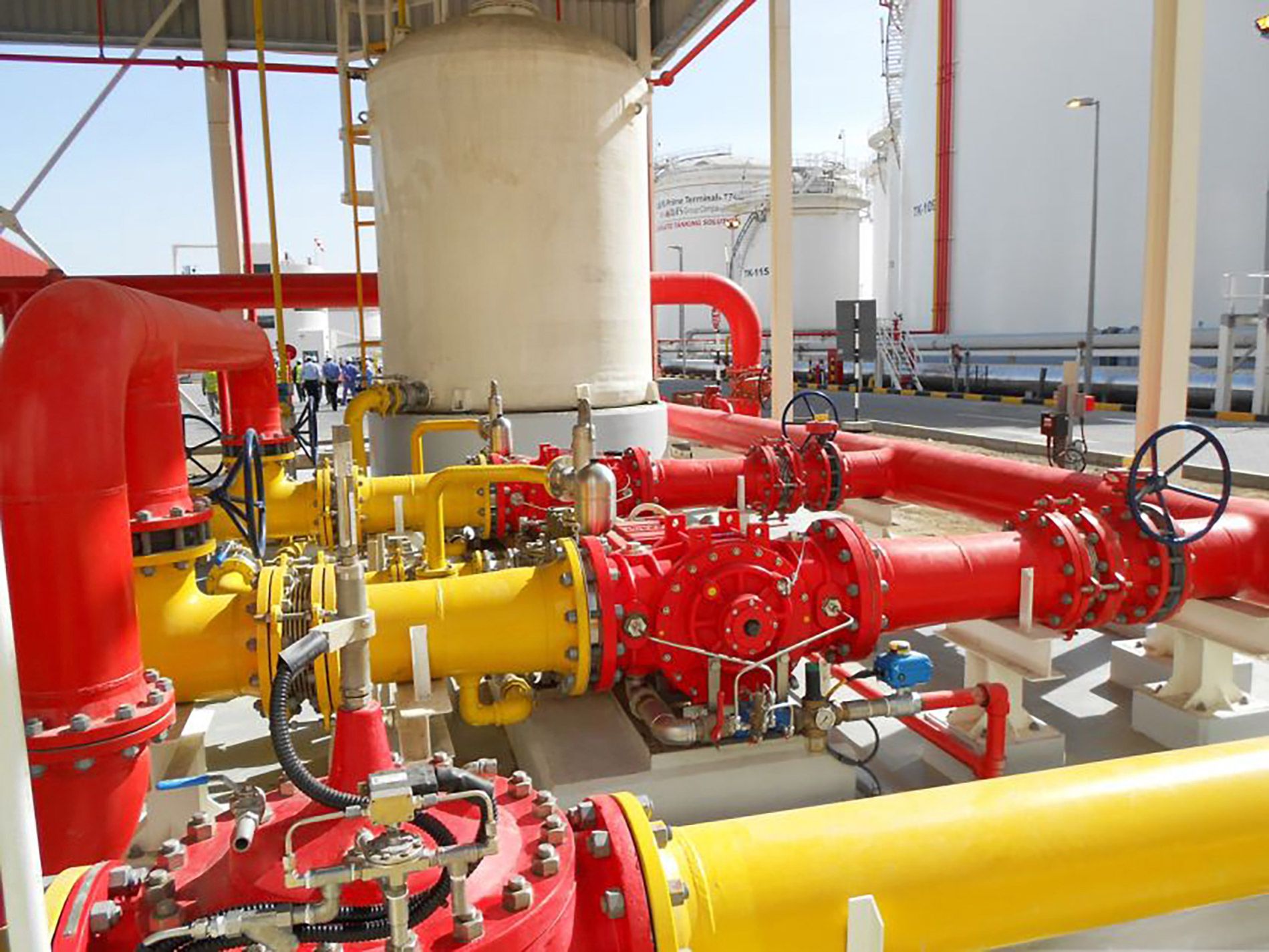
Water motor with proportioning pump
Mobile extinguishing systems
As the stationary foam discharge equipment can be damaged in extensive fires in the tank or in the dyke area and thus lose effectiveness, mobile fire monitors and foam pipes may be used.
Foam pipes
Foam pipes are normally held by firefighters, making them very flexible. Yet they have only limited extinguishing agent flow rates and reaches.
Firefighting monitorS
Firefighting monitors are discharge devices mounted on vehicles or trailers and available in many sizes. The extinguishing agent flow rate can be up to 60 000 l/min and the reach can be up to 180m if the pressure of the fire pumps is sufficient. They are suitable to discharge foam, e.g., to extinguish a surface fire in a tank; or water, to cool down a neighboring tank or the tank wall of a burning tank in order to prevent reaching the critical temperature for a boilover or to keep the flames from spreading. The accumulation of water inside the dyke area should always be observed to avoid an overflow of the dyke.
Mobile fire monitors can be supplied either by the extinguishing water of the stationary fire pumps or by mobile pumps. The injection of the foam concentrate usually takes place via mobile proportioners. This clearly points towards the advantage of energy independence for water motor-driven proportioning pumps.
The strategic decision for the sizes of mobile units available as back-ups is shown by the following example for the placement of monitors for fire extinguishing at tanks which are 45m in diameter and 15m high. According to NFPA, 32 000 l of premix per minute are required. This results in several alternatives for the monitors. Generally, foam concentrate proportioners for at least 32 000 l/min are required, which should be able to handle varying flow rates to guarantee flexibility during extinguishing operations. Depending on the local conditions, the monitors will need to keep a minimum distance to the burning tank or may not be able to be positioned near to the tanks due to debris. In addition, it will not always be possible to position several monitors around the tank. It must be ensured the monitor has sufficient throwing height in relation to the tank height, to deliver foam into the inside of the tank. The dimensioning of the entire fire fighting system is made following legal regulations as well as recommendations by associations like NFPA and ist not looked at more closely in the present article.
Fire monitor size | Quantity | Distance from tank [m]* | Flow rate [l/min] |
M9 | 1 | 95 | 40,000 |
M7 | 2 | 80 | 20,000 |
M5 | 3 | 60 | 12,000 |
M4 | 4 | 45 | 8,000 |
* Distance between monitor and tank dependent on low rate
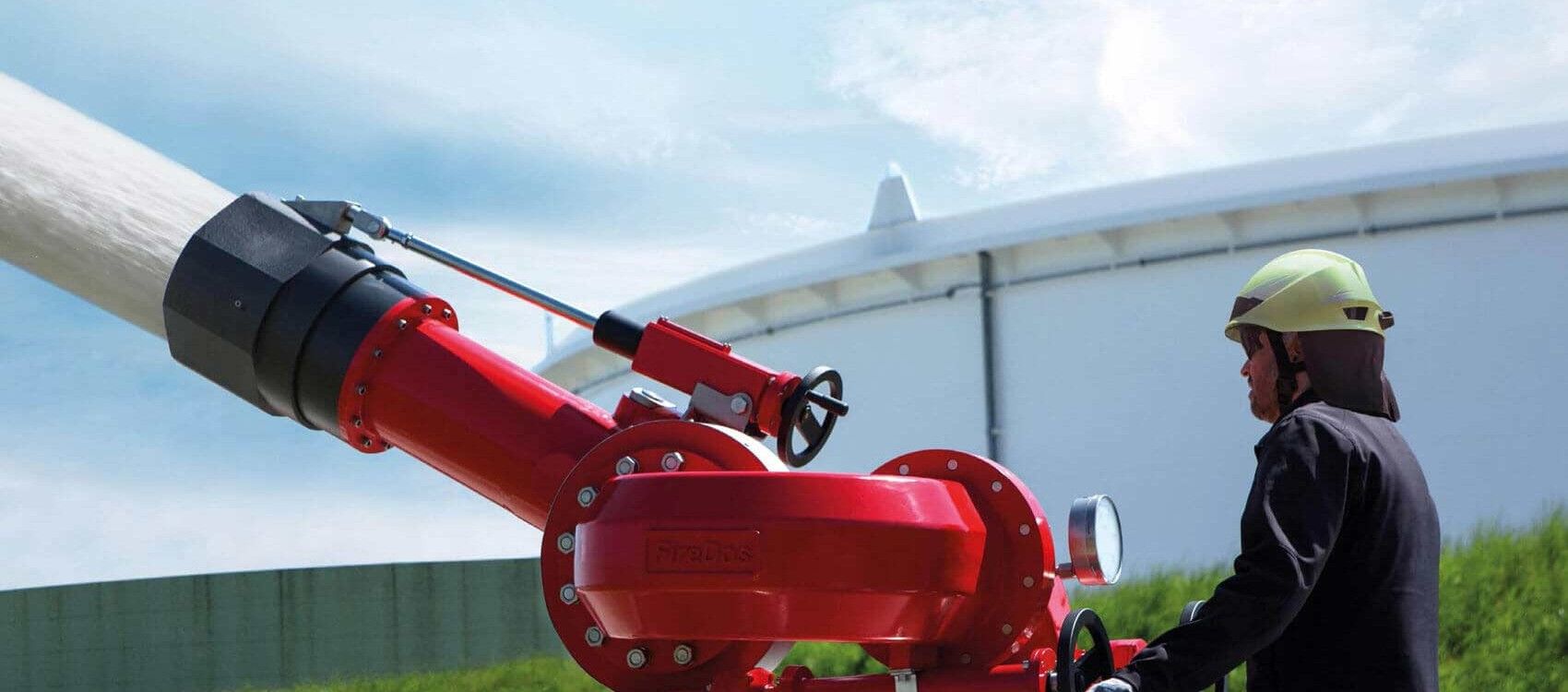
Fire monitor M9 in a test run at a tank farm
Lessons learned
As mentioned in the introduction, it seems that many authorities and companies have not learned the necessary lessons from disastrous fire incidents of past years. Tank farm fires in the oil and petrochemical industry do not happen frequently. When they do, they usually have devastating consequences. Let us remember the tank farm fire at Deer Park, Texas in March 2019 mentioned in the introduction.
The fire developed after over 30 000 l butane-enriched naphtha had been leaking from a faulty valve for 30 minutes and caught fire for yet unknown reasons. The plant had no gas warning system and no remote-controlled valves to shut off the leaking fluid. In addition, some areas did not have fixed extinguishing systems installed. All 15 tanks were surrounded by one single dyke. The owner had relied on the local fire service which was on the spot very quickly but could not take control over the fire with the equipment available, partially because flammable substance was continuously leaking from the tank. 36 hours after the fire had broken out, a contract was made with an external fire fighting company to do the extinguishing work. Mobilization of equipment and foam concentrate as well as the preparation of a plan of action took approx. 13 hours. The fire was finally extinguished after 14 hours of fire fighting, 63 hours after it initially broke out. Extinguishing attempts were made over three days, with foam concentrate and water shortages occurring in the meantime. In total, over 500 000 l of foam concentrate were used. Instead of a fire in the dyke area, 11 of the 15 tanks burnt down.
It is very probable that the fire would have been extinguished quickly if the warning systems and valves had worked and a fixed fire extinguishing system had existed. It is also probable that the fire would have been extinguished quickly if the extinguishing operation, which succeded eventually, had been started earlier. Both cases would have resulted in notably less damage.
Summing up, the following points should be learned as a minimum. As far as they have not yet been implemented, or just partly, they should serve as a basis for discussions about one's own fire protection concept.
- Have a suitable fire protection concept including alternative scenarios which adapt to the given situation regularly
- Always have a sufficient number of mobile extinguishing systems as a backup to fixed extinguishing systems
- Stock a suitable foam concentrate
- Ensure sufficient foam concentrate supply
- Ensure sufficient water supply
- Keep well-maintained, quickly and well-accessible, strategically correctly placed and functioning extinguishing equipment available in a sufficient number
- Have trained personnel available in a sufficient number
- Ensure a quick implementation of a suitable plan of action
References
[1] National Fire Protection Association, NFPA 11 Standard for Low, Medium, and HighExpansion Foam 2005 Edition.
[2] U.S. Chemical Safety and Hazard Investigation Board (CSB), Factual Update Storage Tank Fire at Intercontinental TerminalsCompany, LLC (ITC) Terminal, Published: October 30, 2019.
[3] Nico Zorzetto PhD, Modern Safety Technologies on highimpact mega-fires, GULF FIRE, January 2020
This article is reproduced by kind permission of MDM Publishing Ltd - this article first appeared in the July 2020 issue of Gulf Fire magazine - www.gulffire.com
This might also be of interest for you:
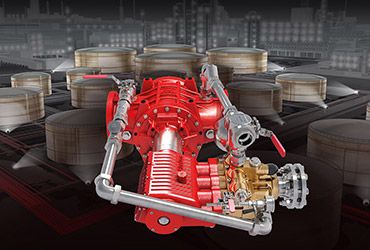
Stationary foam proportioners
Increase performance, save costs: Learn more about the advantages.
View more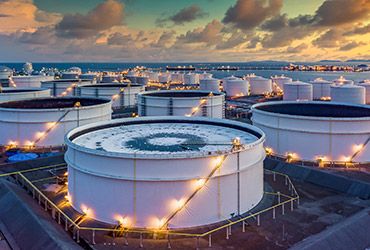
Our solutions for the oil and gas industry
Reducing risks with a flexible fire protection concept
View more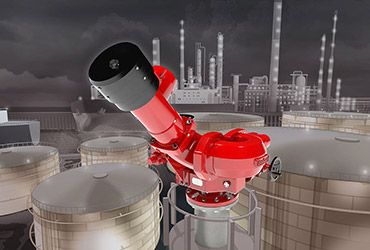
Monitors: Powerful and flexible
Thousands of liters of water per minute, reaching more than 150 meters
View more