Mobile firefighting technology for high hazard applications
Fighting high hazard and storage tank fires is one of the most challenging scenarios firefighters and crisis management teams must plan for and manage. Fixed fire protection systems are increasingly being supplemented by versatile mobile equipment. Industry changes in foam firefighting techniques present some special challenges for equipment manufacturers for a response combining both fixed and mobile equipment.
The occurrence of high hazard fires has reduced in the last few years suggesting training and testing standards have generally improved, supported by testing from industry bodies such as JOIFF and LASTFIRE by sharing best practice amongst the end-user community members. This is an achievement in that global storage capacity is expected to almost double in the 20 years from 2005 to 2025 from approximately 160 billion to over 265 billion gallons.
However, the industry faces increasing challenges and opportunities. These include the legislative & enforced change from environmentally harmful PFAS type foams to Fluorine-Free foams (FFF). The increased use of very-large tanks, more than 300 ft diameter becoming more challenging to extinguish. The oil and gas industry adoption of Industry 4.0 & digital solutions for remote monitoring, control & testing, meaning a reduction in site manpower requirements. Some unknown factors and a reduced level of well-trained manpower means a higher risk.
The use of mobile firefighting equipment which is easy-to-deploy and use will become more important as an integral method to fight large fires as the cost and complexity of fixed systems increases. Fixed systems will always remain a central hub of any fire protection system, but fires break out often due to unknown and uncontrollable events and fixed systems may get damaged by the fire incident itself, calling for some level of flexible response.
Fixed systems
Fixed systems typically consist of a fire water main pump feeding a hydrant or ring line with fixed monitors, foam pourers for tanks and sprinkler systems for storage areas. The foam concentrate is stored in a fixed atmospheric or pressurized storage tank, with a proportioner to deliver the recommended mix of foam concentrate into the extinguishing water stream.
Modern fire protection systems have introduced a degree of remote & automated operation such as flame and heat detection, as well as remote control, ensuring personnel are kept out of harm’s way as much as possible.
The selection of equipment varies, often with a trade-off in terms of operating cost, performance, reliability, testing and size. Due to the large size, complexity and cost of fixed firefighting equipment, operators and end-users are increasingly looking to provide hybrid solutions. The ideal being a fire protection system using a fixed system aided by a team with versatile mobile equipment which can be rapidly deployed, depending on the hazard.
Mobile firefighting equipment
Mobile firefighting equipment primarily includes the use of high-capacity monitors and associated equipment, such as hoses and hose laying equipment, and where necessary foam tankers & proportioning equipment.The challenges for many mobile applications are the potentially long hose lengths, restricted diameters and the pressure drop associated with many pieces of equipment.
Bladder tanks & balanced pressure proportioner systems combined with venturi-based proportioners (eductors/inductors) or wide range proportioners are designed for fixed installations with a fixed range of pressures and flows. Typically, they are easy to design and install but like all engineered systems, there is a trade-off. One of these is their lack of suitability for mobile applications and varying firefighting approaches.
Venturi type proportioners, including jet ratio controllers are not suited to modern mobile applications when faced with non-Newtonian high shear-rate and high-viscosity foam concentrates. Foam proportioning rates become more important, especially with FFF foam concentrates, as Venturi’s cannot guarantee a specific proportioning rate at varying water flows.
Foam pumps are also only suited for fixed installations due to their need for external power, such as electronic control units and an electric motor or diesel engine. The ideal design for mobile equipment are components that are external power independent with a low pressure-loss, consistent proportioning rates irrespective of foam concentrate viscosity at varying water flows and back pressures, that are easily and rapidly deployed.
Mobile proportioner design
The two main criteria of any foam proportioner is proximity to the foam concentrate source and its pressure loss. If foam proportioners can deliver the required foam rates without large pressure losses to monitors, mobile systems become more attractive to system designers and firefighters alike. FireDos GEN III hydraulically driven foam proportioners present significant advantages:
Accurate proportioning rates
The water from a hydrant or ring main is used to drive the positive displacement water motor, which in turn drives the plunger pump of the foam proportioner. As each revolution of both the water motor and proportioning pump have a fixed volume, we can easily determine the fixed proportioning rate. As the water flow increases through the water motor, this in turn increases the volume of foam concentrate pumped into the outlet of the water motor & into any mobile foam outlet devices such as monitors and hoses. Unlike other proportioners, the FireDos GEN III is entirely independent of the system pressure and will generate the required proportioning rates independent of any system pressure & flow fluctuations.
Testing
The cost of operation of any foam extinguishing system must consider the ongoing foam proportioner testing costs, including any clean-up and disposal costs. Having the ability to circulate the foam concentrate back to the foam concentrate tank is a major saving provided by FireDos GEN III proportioners. This eliminates any short- or long-term environmental impact, such as associated disposal and even mobile foam testing can comply with NFPA11 testing requirements.
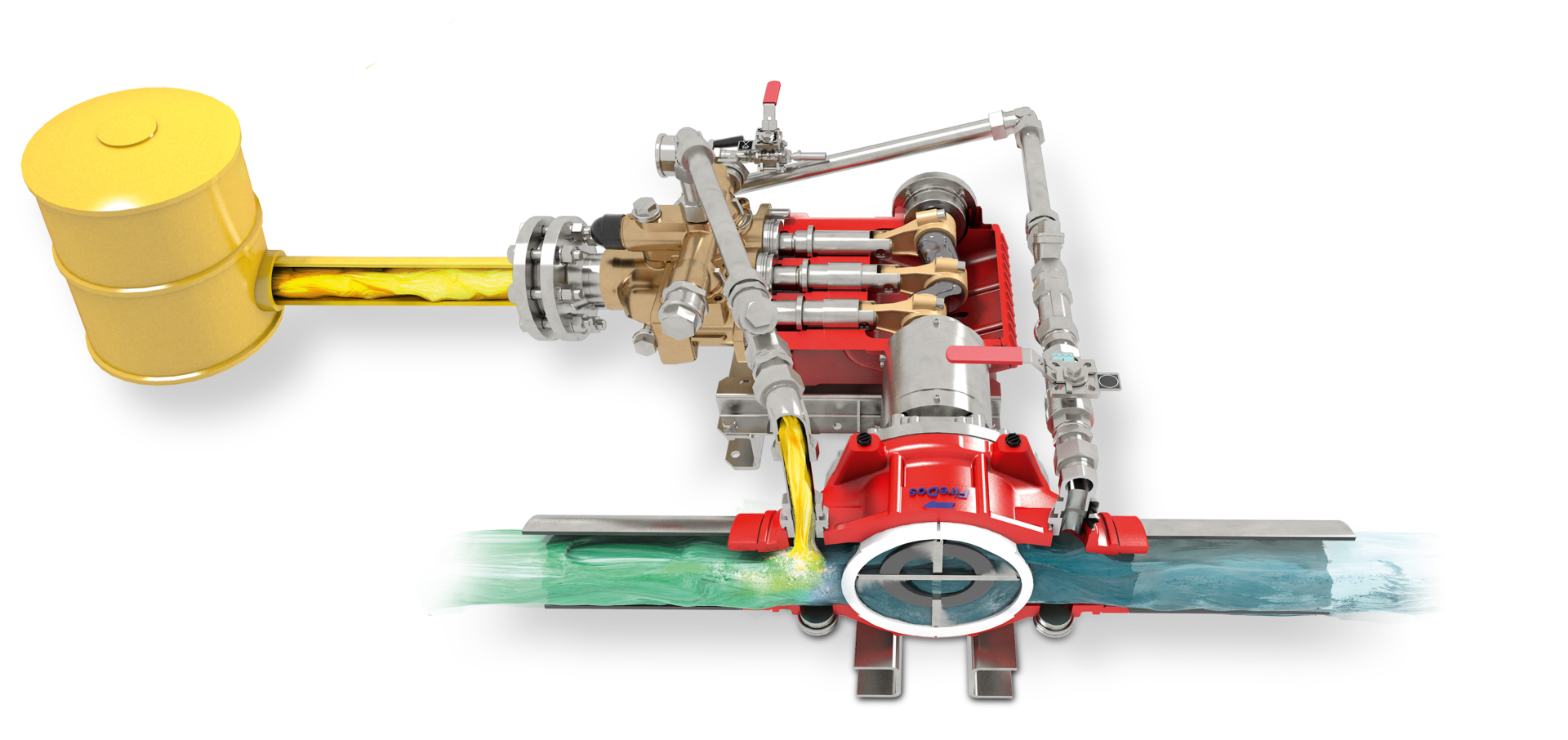
Figure 1. FireDos GEN III method of operation including test function recirculating foam concentrate to the foam concentrate tank.
Capacity limitations
It is common to locate the foam concentrate tank, proportioner and monitor together on the trailer. The size of an Intermediate Bulk Container (IBC) tank typically contains 265 gal of foam concentrate, providing a limited firefighting capability. For small applications up to 265-530 gal extinguishing water with a 3% nominal foam proportioning rate, an integrated trailer could provide up to 17 min. at full flow. At a 1% nominal proportioning rate this is triple the time (up to 50 min.). The use of an integrated trailer solution offers the advantage of rapid deployment, as additional foam concentrate supply can be organised separately.
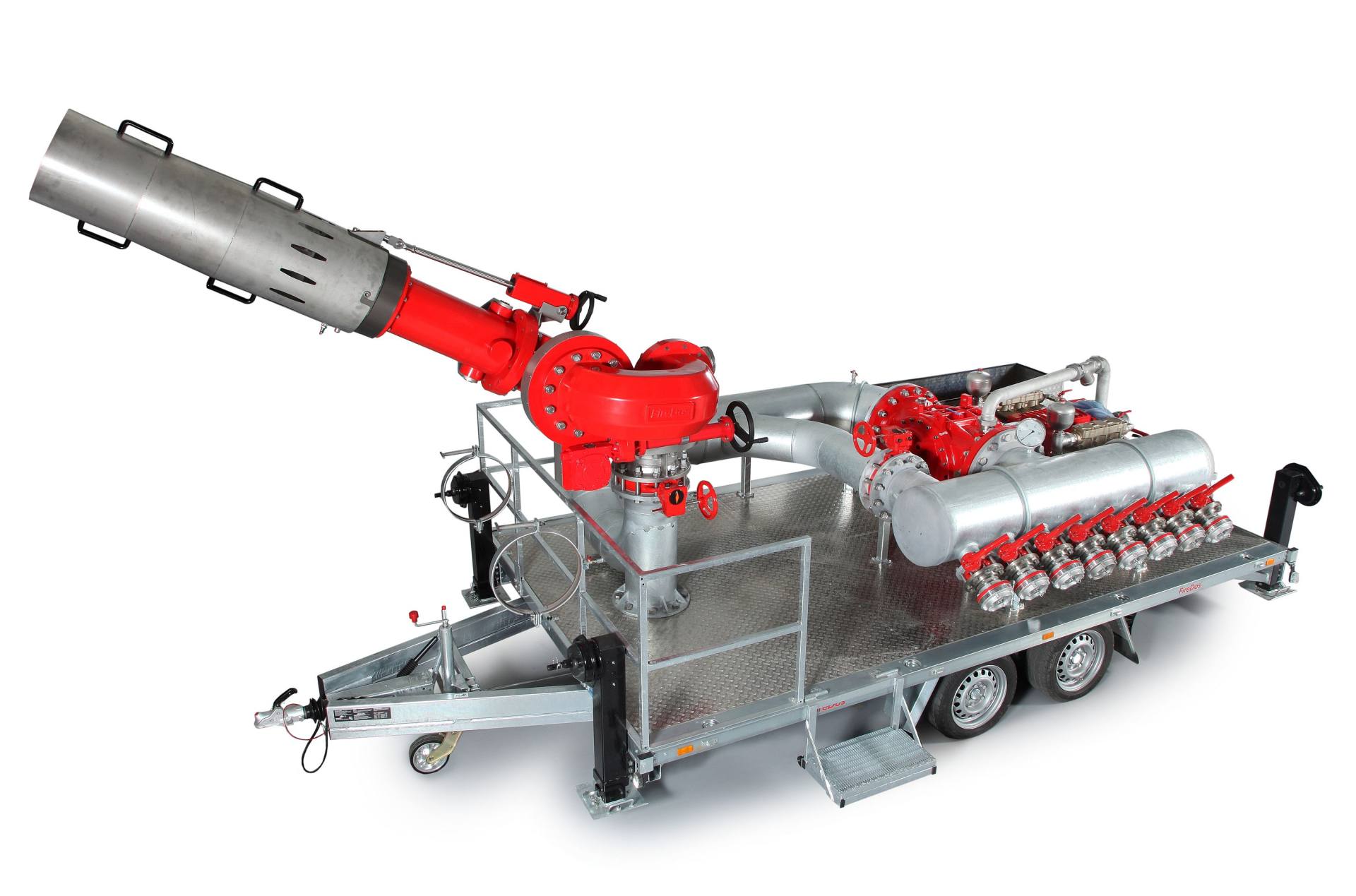
Figure 2. Integrated monitor & foam proportioner trailer: FireDos M9 & FD20000 up to 5200 GPM
For medium water flows above 530-1055 gpm, separate mobile proportioners fed by foam concentrate tankers are recommended. This aids in the rapid deployment and setup as the position of a monitor is not dictated by the location of the bulk foam concentrate supplies or the accessibility of a foam concentrate tanker. The versatility of FireDos foam proportioners means they are not susceptible to changes in back pressure or flow restrictions, guaranteeing foam quality at the specified percentage regardless of flow rate.
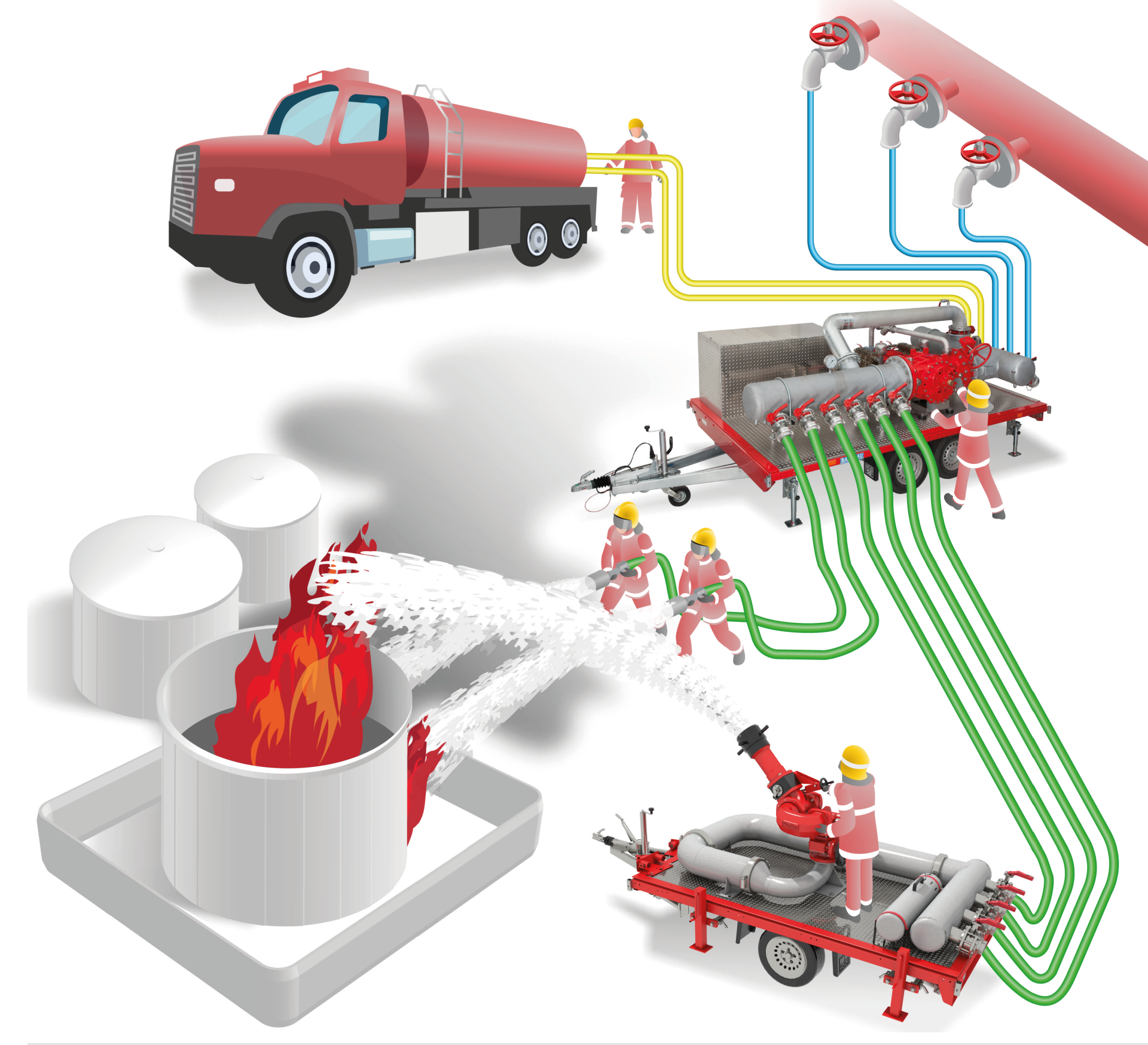
Figure 3: Typical FireDos water driven foam proportioner fed by a foam concentrate tank feeding a trailer mounted monitor and 2 hand nozzles fighting a tank fire and bund protection
Foam concentrate viscosity
Depending on the type of foam concentrate, the foam concentrate viscosity, proximity to the proportioner and foam concentrate suction piping diameter and design can all have an adverse effect on the performance of any foam proportioning system. At FireDos, as manufacturers of foam proportioning equipment, we see many applications regardless of proportioner type, where the foam concentrate suction line to the proportioner is designed without adequate consideration of the above-mentioned aspects, resulting in ineffective foam systems. Unlike low viscosity foam concentrates such as AFFF, most new FFF are non-Newtonian, pseudoplastic and highly viscous. The FireDos GEN III is designed to overcome the challenges in the handling of high-viscosity foam concentrates.
Pressure loss
The pressure loss of an extinguishing system can be the difference between a system working or not. This means careful consideration must be taken for the firewater-main pressure, the maximum hose lengths and equipment such as the monitors and proportioners. The GEN III is designed with a maximum pressure drop of up to (21-27 psi, dependent on operating conditions. A low-pressure drop across the proportioner, combined with an ideally designed monitor, mobile mounted equipment becomes a more attractive option.
Ideal Monitor design
Firefighting monitors for mobile use should be easily transportable, rapidly deployed, easy to operate with a low-pressure drop from inlet to the nozzle. FireDos introduced their range of FM approved firefighting monitors for water and foam with flows ranging from 132 gpm at 90 psi to 15,850 gpm at 232 psi. Each model is designed using the following characteristics for trailer mounting:
Low-pressure drop, balanced design
Long lengths of hose and associated equipment such as foam proportioners, ‘rob’ much-needed pressure to deliver monitors and nozzles the pressure required to develop a reasonable throw and reach wanted to keep personnel out of harm's way and to reach the intended target. This is especially important on large storage tanks. FireDos redesigned the internal monitor pipework using a Computational Fluid Dynamics program to minimise flow restrictions & came up with the “Oval-flat” design, which led to a class-leading pressure drop of less than 14.5 psi at full flow and therefore a longer throw and reach.
No ballast tank required
The design of the majority of other monitors necessitate the requirement for a big ballast tank to stabilize the trailer. A big ballast tank takes time to fill, empty and adds a ‘dead-weight’ making trailer movement and re-deployment difficult. The balanced design works to counteract these forces by acting upon itself to balance the pressures out, thereby minimising the reaction forces. The reduced ballast needed is created within the optimised monitor inlet piping. By sizing the piping on the trailer accordingly no additional ballast tank is necessary, aiding in rapid deployment and accessibility to more varied terrain.
Adjustable flow during operation
When fighting different classes of fire with newer foams (FFF) with varying drainage times, changing flow during operation means more rapid control of a fire hazard situation. Many monitor designs must be switched off and isolated to change the flow, delaying the firefighting effort. Enabling the flow to be changed by means of a handwheel mid-flow, as with the FireDos AMPN nozzle, without stopping and isolating during continued operation of the monitor also means the firefighting operation is not interrupted.
If a “banking or raindrop” type of firefighting attack is required, as is sometimes recommended for type III methods, adjusting the flow midstream provides an added advantage. A more accurate flow-stream footprint can be obtained by modifying the angle of attack, combined with altering the flow based on weather conditions.
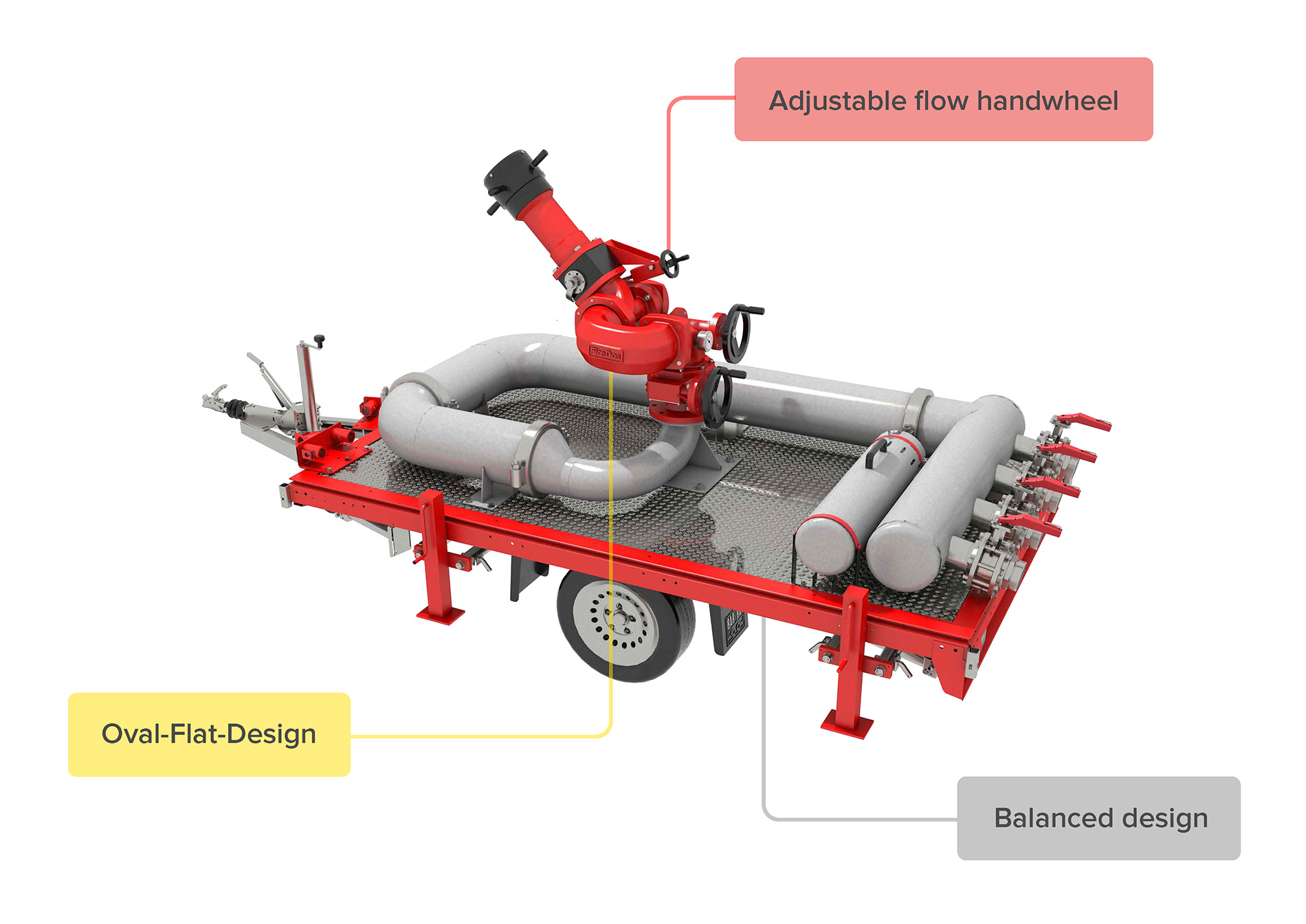
Fig 4. Trailer mounted proportioner & monitor design
Conclusion
The reputational damage associated with large fires is often worse than the tangible costs as the PR costs often outweigh the physical costs. Modern operators now must consider the costs of foam discharges and any short- or long-term damage to the environment.
Utilising equipment designed for mobile use, rather than modifying equipment initially designed for fixed extinguishing systems is one such method to achieve better outcomes.
Mobile firefighting equipment, ideally designed for rapid deployment & ease of use means less manpower is required to operate and with longer throws and reaches, keeps firefighters further out of harm’s way.
Ultimately, modern approaches to designing hardware using CFD & FEA techniques making them easier to operate and faster to deploy, with features such as integral testing without discharging foam to the environment or changing flow rates during operation, means the industry is safer & more responsive than ever before.
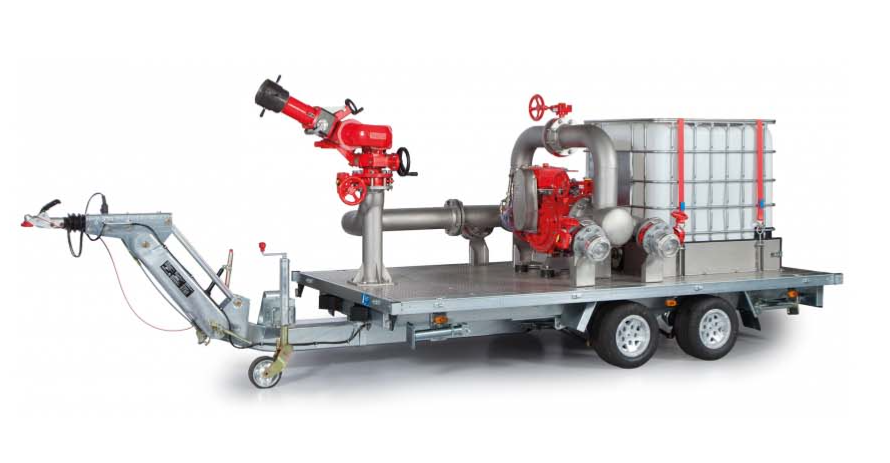
Fig. 5: Integrated foam storage tank, foam proportioner & monitor trailer for small applications: FireDos M3 up to 4000 LPM .
This may also be of interest to you:
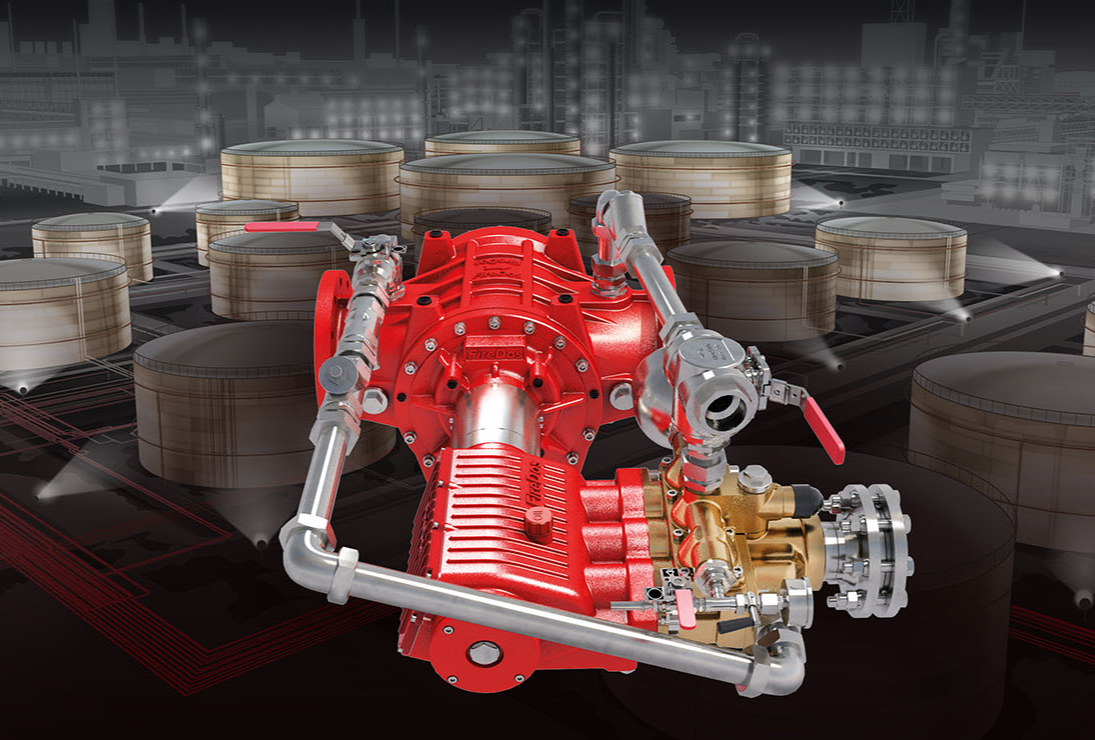
Stationary Foam Proportioners
Inrease performance, save costs: Learn more about the advantages.
View more
Our solutions for the Oil & Gas industry
Learn how to reduce risks through versatile fire protection systems.
View more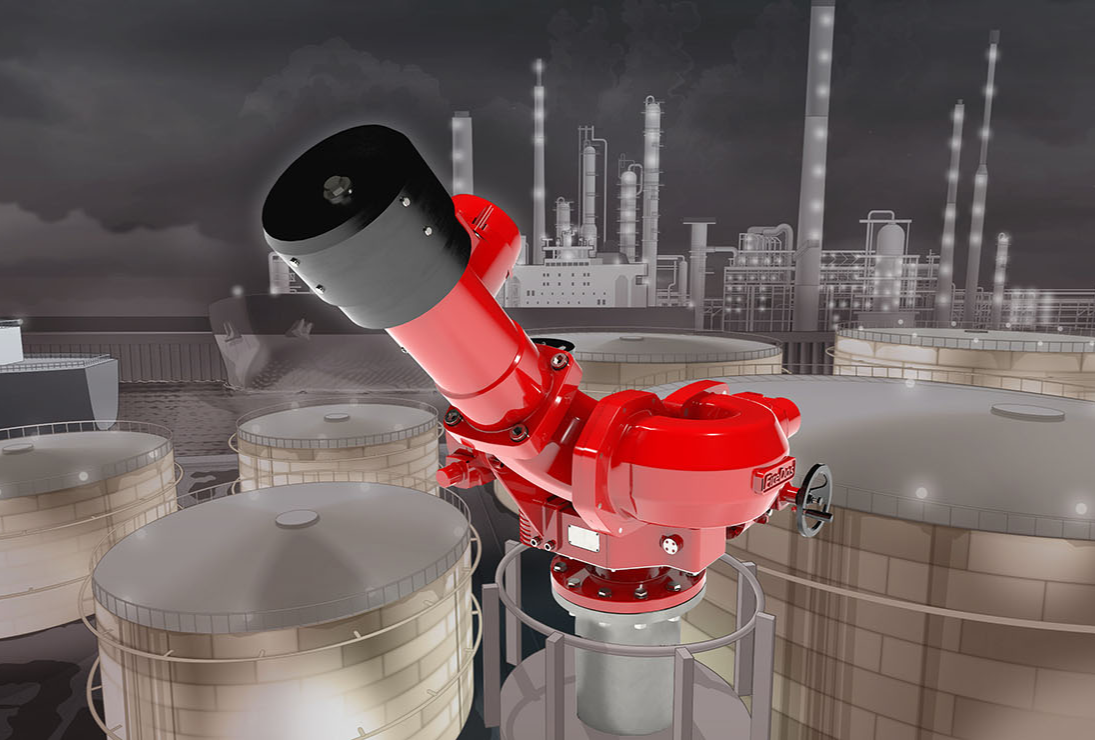
Monitors: Powerful and flexible
Thousands of liters of water per minute, reaching more than 150 meter.
View more