Advanced hybrid firefighting solutions for major fire hazards
Firefighting technology is constantly advancing. This case study illustrates the latest technology in mobile firefighting equipment developed by FireDos for class B high hazard fire scenario applications, including tank storage facilities, refineries and other oil and petrochemical related industrial fires.
Major tank storage fires, although statistically not a major hazard to life, present a major hazard to the environment, the loss of physical assets and a firm’s reputational assets. Lightning strikes cause the majority of tank storage fires. However, in recent years we have seen many other causes, such as Hot work and even missile attacks.
Whatever the cause, a hybrid response is required with a mobile backup system because the stationary system is damaged. This relies on the efforts of an onsite firefighting team or, in larger areas with multiple companies, a shared, mutual or unified firefighting team. Firefighting technology is constantly improving, becoming more efficient, versatile and safer to fight fires, ensuring the hazard to life and lost assets are minimized.
The following is a case study of one such firefighting method, ideal for use as a rapid response and versatile solution that overcomes some of the challenges firefighting equipment faces, such as different foam concentrate characteristics and minimizing the task burden on firefighters during the stress of a fire event.
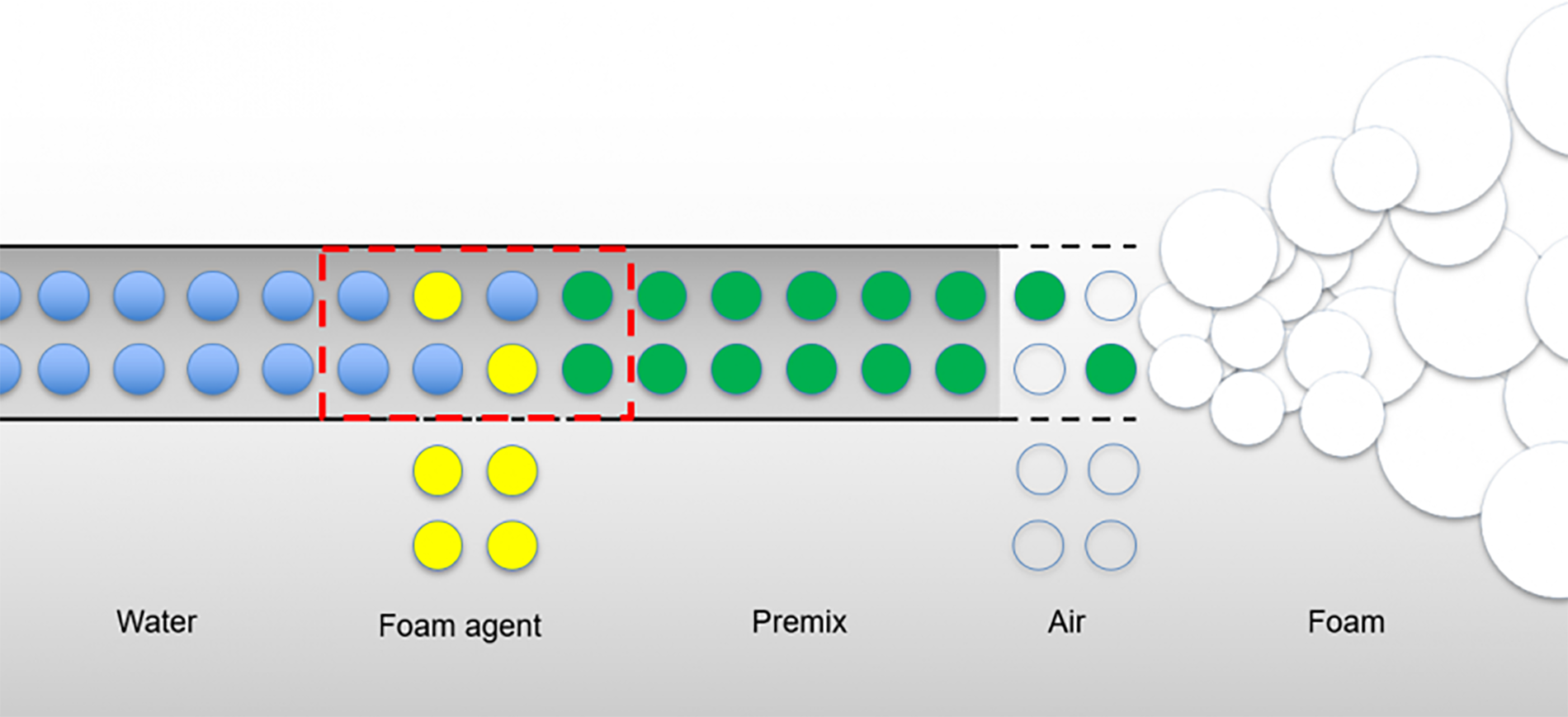
Storage tank sizes increasing in size and quantity
There are approximately 5,000 tank farms in existence worldwide. This number is increasing through globalization and tank technology, enabling larger diameters and increased storage capacities. As a result, many new tank farms have tanks larger than 300 ft (approx. 100 m) in diameter. This presents an additional problem for firefighting due to the volume of flammable fluid, equipment considerations and accessibility, such as monitor range.
Hybrid system design challenges
The term hybrid system means a fixed firefighting system, such as the combination of fixed foam pourers, chambers and monitors fixed to a facility, combined with a mobile backup equipment conveniently positioned to knockdown and extinguish the fire as rapidly as possible. Existing mobile equipment is usually in the form of trailer-mounted firefighting monitors connected to a foam tank and a water supply. Mobile firewater pumps or a hydrant system might deliver the water supply. In addition, hose-laying equipment, proportioning pump skids and foam tankers to deliver the high volumes of foam concentrate necessary for a significant firefighting operation are required.
Existing mobile monitors are usually fed by jet ratio pumps and require additional adjustment based on the flow rates of interchangeable baffle plates. The major disadvantage of the existing mobile high flow monitor approach is complexity. Response time is essential with any significant fire hazard. In addition, making slide rule or complex calculations to account for hose lengths, elevation, flow rates and pressures increases the possibility of human error.
All these issues combine to make an ineffective foam quality, which is at risk of being unable to extinguish a fire. From our collective experience at FireDos, as firefighting monitor manufacturers, most high-flow self-educting monitor trailers become rapidly redundant due to their complicated use and ineffectiveness in providing a consistent foam quality needed for effective fire extinguishment.
Proportioning technology within trailer-mounted systems
Traditional high-flow self-educting foam monitors are fed foam solution using multiple jet ratio pumps, required for additional foam-rich solution mixing before being fed into the nozzle inlet of a high-flow monitor at the required proportioning rate. This presents several challenges as the hose pipework and jet pumps required multiply as the flow rate increases. The differing flow rates and pressures mean the number and type of jet ratio pumps must be calculated in advance. Furthermore, the pressure loss of jet pumps means a high inlet pressure is required for effective operation.
The complexity of managing numerous jet pumps and the calculations required increase the possibility of human error. All the above contribute to the possibility of ineffective foam quality and, therefore, the inability to extinguish the fire effectively.
Designing for better reach with a given flow and pressure
Existing monitor designs are generally of two or three pipe elbows welded together, ending in the outlet of the monitor nozzle.
The flow through an elbow increases fluid turbulence. Turbulence is the equivalent of pressure loss across a monitor from the inlet to the nozzle outlet. The higher the pressure loss, the shorter the throw and reach for a given pressure and flow.
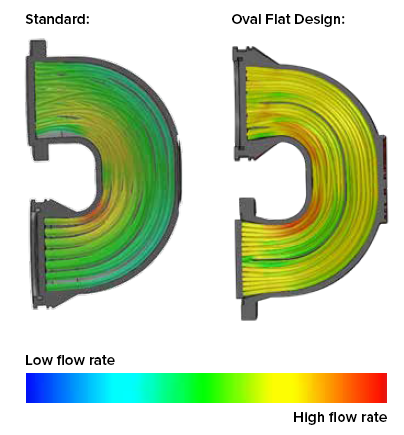
Variable, stepless flow rate adjustment
Generally, high-flow monitors are set up with an interchangeable baffle plate dependent on the given flow rate and range required. If the flow rate needs to be changed while keeping the optimum angle of attack, the monitor needs to be taken out of action before the baffle plate is changed to suit a new flow rate. This is important with polar solvents (alcohols, ethanol) as a gentle banking approach (class III) is required to prevent the foam from plunging under the surface of the burning fuel and subsequently getting damaged or picking up fuel and burning on the surface. Eliminating the requirement of independent fixed-flow baffles with an internal movable baffle means the flow of FireDos monitors can be adjusted steplessly.
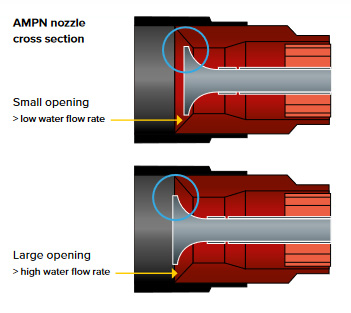
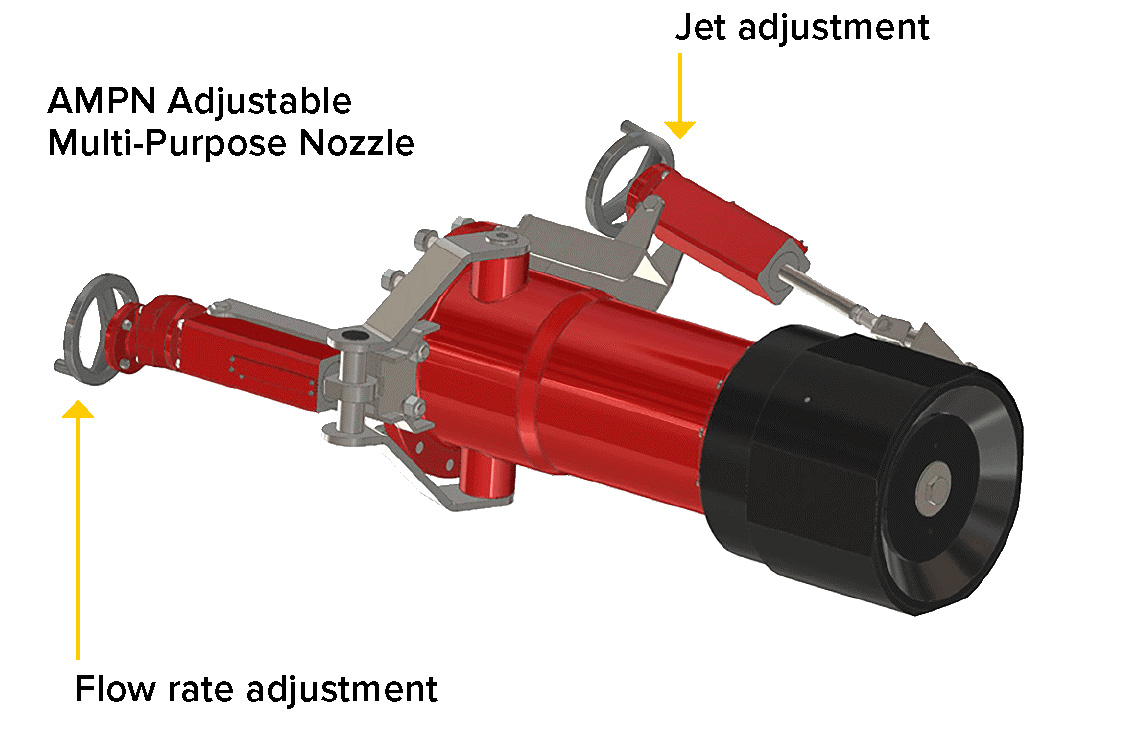
Making the ballast tank redundant
The reaction force in a monitor throwing 10,582 GPM (40,000 LPM) at 10 bar (145 psi) is 30kN or 306kgf, which is considerable, and therefore needs some form of ballast to prevent the monitor trailer moving in the opposite direction. The unique design of the self-balancing pipework of FireDos monitor trailers eliminates the need for a ballast tank as the pressure counteracts its forces within the trailer design. The self-draining monitor design reduces the possibility of stress-corrosion and enables rapid and effective movement of the trailer. All these design elements assist by minimizing the stress on operators due to their simplicity and ease of use with an increased throw range.
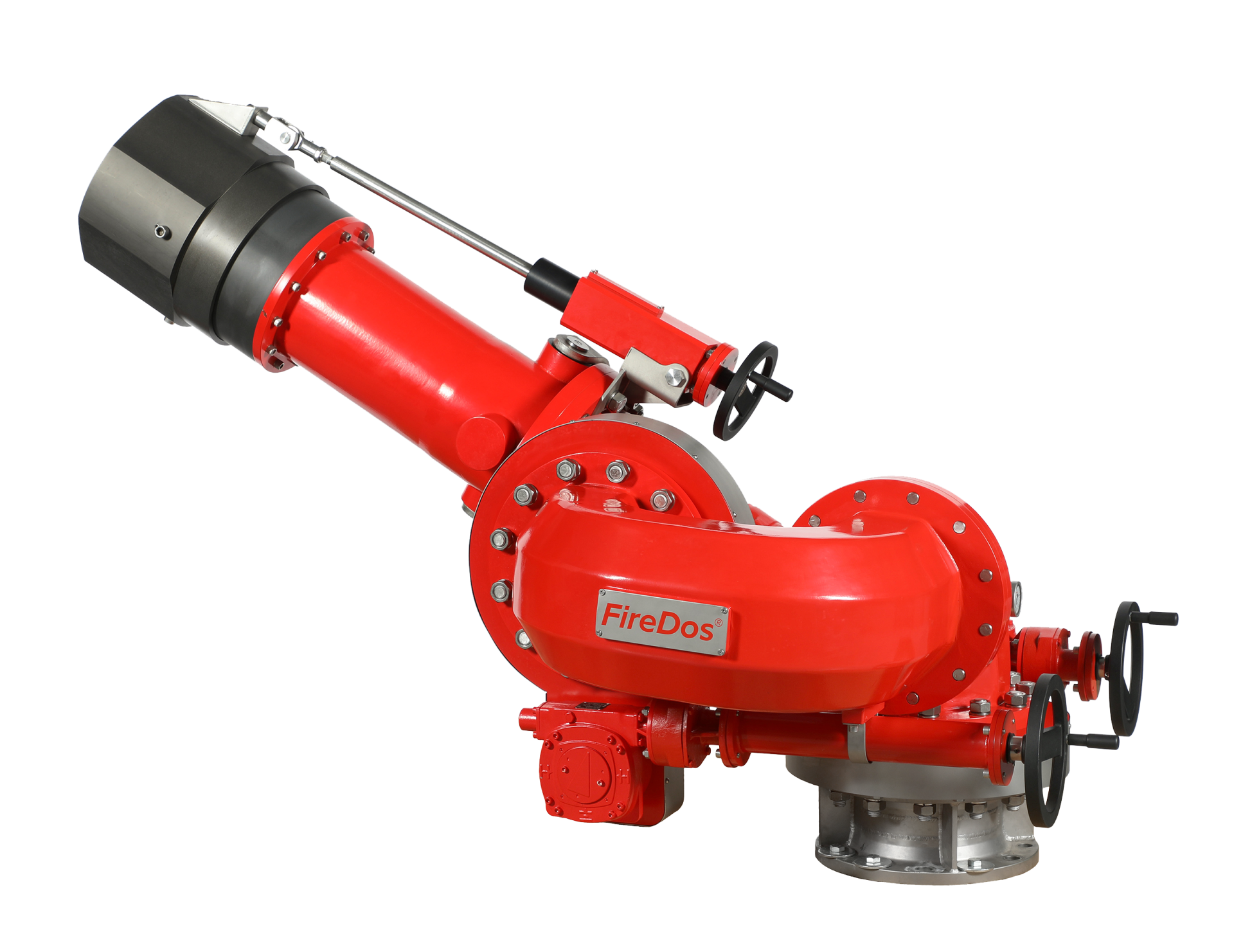
Oval flat design using CFD significantly improves the flow through the monitor
Minimizing hose lengths
Hose lengths and quantity of hoses increase the human stress on any deployment. Therefore, response time is minimized by utilizing maximum diameter hose lengths and efficient hose deployment vehicles. Increased hose lengths reduce the efficiency of a system, combined with jet pumps, which means the need for intermediate pumps is required or, therefore, affects the throw reach of a monitor. In addition, jet pumps generally require a minimum pressure to operate effectively. Combined with hose deployment vehicles large-diameter hoses are automatically laid and retrieved to reduce the stress on firefighters.
A case study solution
A recent case study for FireDos came up with the following solution for a major oil industry end user. Connected to a hydrant system, hose lengths are up to 1,000 ft (300m). The hydrant pressure is 174 psi (12 bar) with flows of 8,000, 10,000 and 12,000 GPM (respectively 30,240 LPM, 37,800 LPM and 45,360 LPM) through a trailer-mounted, water-driven variable-flow foam proportioner suitable for foam proportioning rates of 1% and 3%, utilizing an AR-AFFF foam. The foam proportioner can be positioned for convenience anywhere along the length of the hose layout, due to the unique capabilities of water-driven foam proportioners unaffected by hose back-pressure or varying flows. This is a further advantage when using adjustable flow monitors as the proportioners easily meet the needs of variable flows.
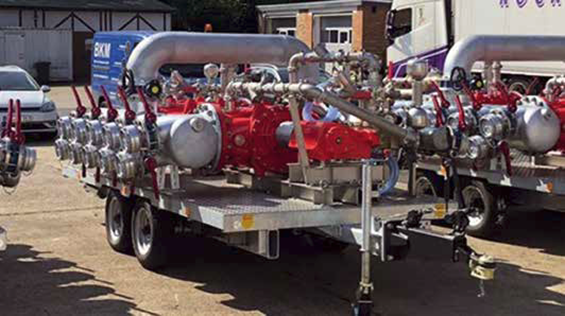
Variable flow, foam proportioner trailer – up to 13,225 GPM (50,000 LPM)
The low hydrant pressures and long hose lengths are not a major issue for the foam proportioner, as the foam proportioners present a low pressure loss of less than 29 psi (2 bar). An equivalent 174 psi (12 bar) inlet to a jet ratio pump would result in an approximate 58+ psi (4+ bar) pressure loss.
The foam proportioners are feeding monitors with capacities up to 15,873 GPM (60,000 LPM). The limiting factor being the maximum flow rate through the proportioner is 13,227 GPM (50,000 LPM). Two 5,280 gallons (20,000-litre) capacity foam concentrate tankers are available to feed the proportioners with foam. The monitor trailers are ballast free and self-draining, ensuring rapid deployment and redeployment. The flow rate is variable during operation, enabling fine adjustment of the footprint of the jetstream during operation and the ability to easily ‘bank’ the foam application, minimizing foam damage and therefore improving the likelihood of a successful extinguishing attempt.
All of the above challenges have been addressed with this system solution to provide a guaranteed foam proportioning rate to suit the application, low pressure loss and optimized design to maximize the throwing reach with a variable flow pattern for the fire protection of some of the largest tank sizes in existence.
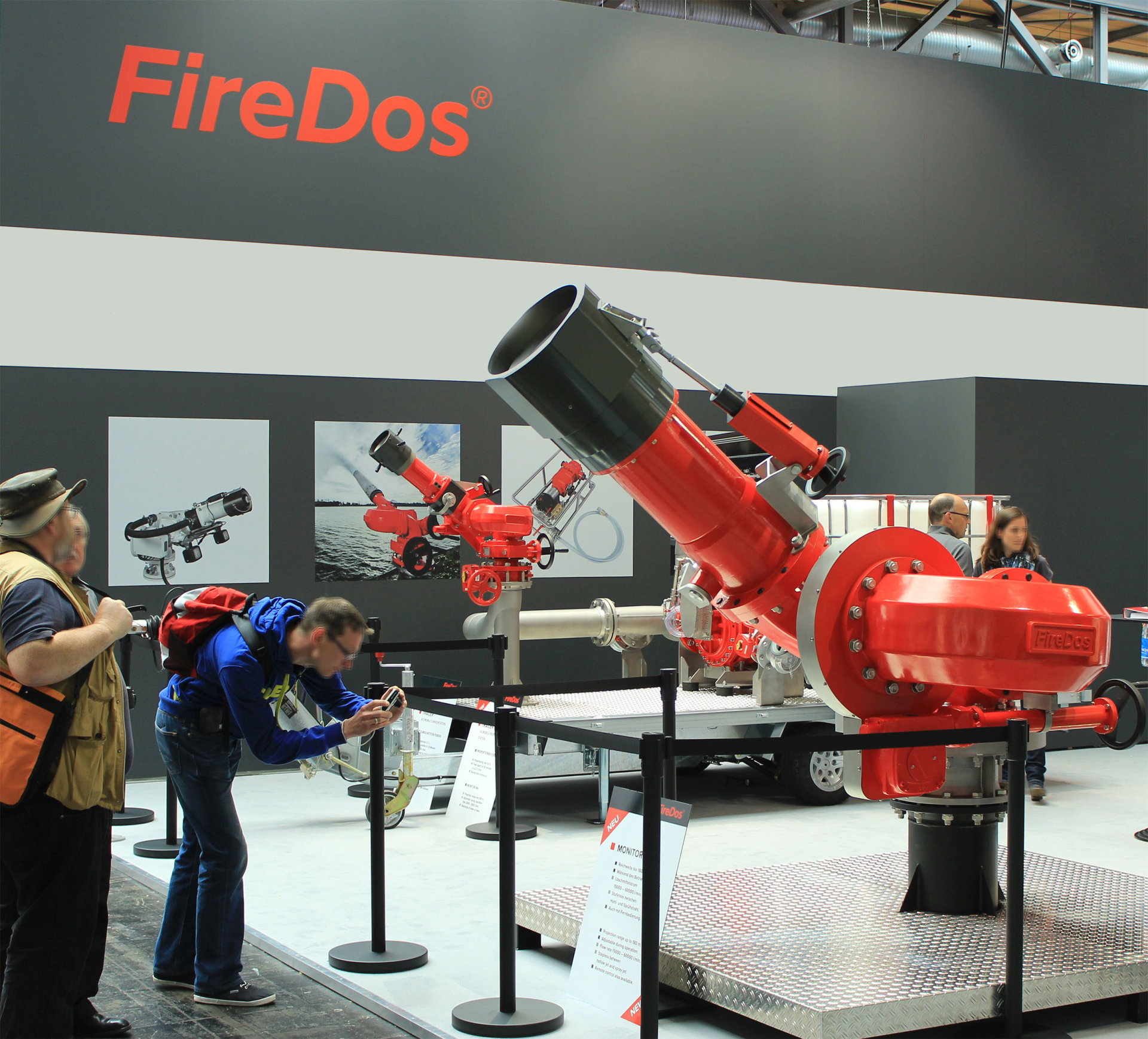
FireDos M12 monitor with stepless variable flow, non-ballast, jet and fog