Extinguishing foam is key
Extinguishing foam is seen as a complicated firefighting method even though flammable liquid fires only account for around one in five fires. When they occur, they are particularly hazardous, so using foam correctly for extinguishing is critical and foam is the most critical component of a firefighter’s tool for class B fires. FireDos’ philosophy of ‘Proportioning in Excellence’ is enshrined in the manufacturing of precise foam proportioners and monitors designed to dispense foam accurately, regardless of the flow or pressure. This article helps to understand how it works, the equipment needed to proportion accurately, and the latest developments in foam firefighting equipment.
Using firefighting foam means proportioning, admixing, or dispensing it at the manufacturers and regulatory bodies (NFPA 11, BS EN13565, FM global, ICAO, UL162, IMO, MIL-F-24385) recommended proportioning rates. A common misconception is to increase the proportioning rate because a thicker mixture allegedly extinguishes the fire more rapidly. Firefighting with foam and the associated extinguishing or suppression devices have developed substantially over the past few years. The advantages of foam-based firefighting are the ability to quickly smother a potential hazard and effectively knock down an oil/chemical-based fire.
Foam successfully operates by:
- Forming a blanket, smothering, and preventing oxygen from fueling the fire.
- Eliminating flammable vapors released from the fuel surface.
- Separating the flames from the fuel.
- Cooling the fuel surface and surrounding area, such as adjacent tanks.
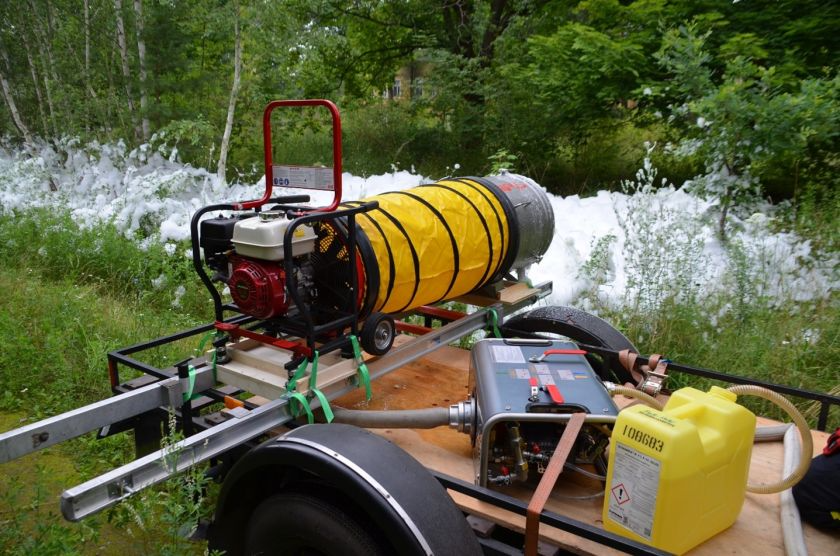
High expansion class A foam being used as a wildfire barrier
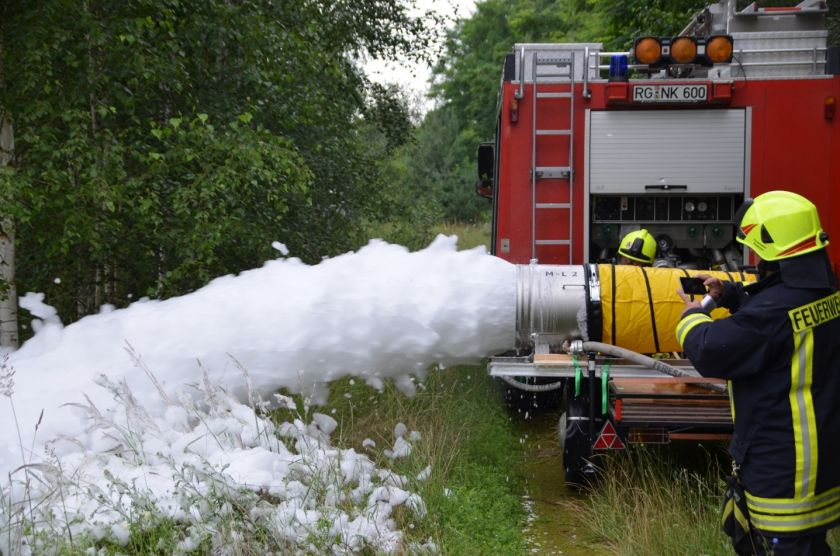
Equipment manufacturers have successfully automated foam proportioning systems to reduce the stress on firefighters having to make mental calculations for application rates and required foam concentrate quantities. However, this has disadvantages in that the systems can be inadvertently abused, thus sometimes making the foam solution ineffective, for example, cycling handline hoses on/off with electronically controlled proportioning systems, as the foam quality is difficult to reach.
Many new and existing foam concentrates come with varying characteristics, such as high-viscosity, pseudoplastic and non-Newtonian, with differing viscosities at different temperatures, and shear-thinning, as the foam viscosity decreases the more it is agitated. Other considerations are air entrainment and sedimentation, and the introduction of environmentally friendly, fluorine-free foams, technically known as Synthetic Fluorine Free Foams (SFFF). Foam concentrate type and selection should of course affect the selection of foam proportioning method, as the flow range, system pressure and mechanical mixing method all influence foam quality.
Proportioning rates and their importance
Typical foam proportioning rates for class B fires have been in the 1% to 3% range. Recent years have seen a steady migration to move to 3% (Alcohol Resistant and Aqueous Film Forming Foams (AR-AFFF/AFFF) with some 1% in use. However, as many existing firefighting foams in use are known to be hazardous to health and the environment, their replacements, SFFF, are generally proportioned at 3% until the foam concentrate technologists develop them further to reduce the proportioning rate. The PFAS (per- and poly-fluoroalkyl substances family) debate and development of suitable tested biodegradable firefighting foams is ongoing and has an important impact on the use of firefighting foams in legacy and new equipment.
Accuracy
The purpose of a specific proportioning rate and why regulatory bodies insist on strict nominal proportioning rates of 3%, with a minimum of 3.0%, a maximum of 3.9%, means a tolerance of -0% to +30% is to maintain the effectiveness of the foam. With lower proportioning rates, there may not be enough active foam ingredients for extinguishment, and the discharged foam solution cannot form an effective blanket to both extinguish a fire and prevent re-ignition. If the proportioning rate is too high, the foam blanket is too thick and cannot travel fast enough across the surface of a liquid to extinguish.
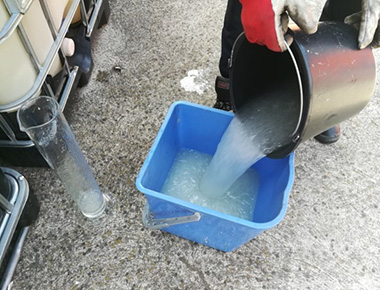
An experiment with a high-viscous foam agent.
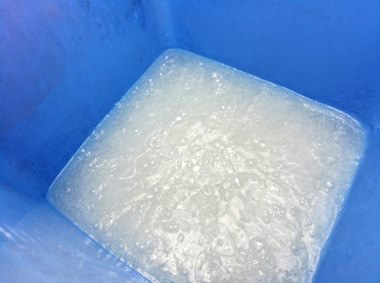
Handling the foam agent leads to air trapping.
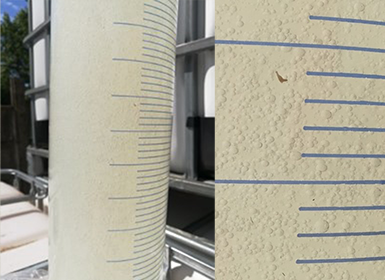
Filling the foam agent into a transparent pillar makes the air trapping visible.
Extinguishing time
For an end-user or fire brigade, the obvious advantage of a lower proportioning rate is the ability to make the available stored foam last longer. A foam proportioning rate at 1% lasts three times longer than a 3% proportioning rate at a given flow rate. For example, a typical fire truck with 2000 gallon of water and 520 gallon of foam equates to 16 minutes of 3% foam solution at a flow of 1050 GPM, assuming a backup supply/hydrant is available for water (otherwise, it is two minutes). For a proportioning rate of 1% foam solution, 48 minutes is available.
Air entrainment in a foam concentrate can also have an impact as the air volume at a system pressure of 145 psi is ten times less than at atmospheric pressure. What does this mean in practice? When a foam concentrate of high viscosity contains 5% trapped air at a system pressure of 145 psi, the foam solution has 0.15% of air under pressure. When this expands upon reaching atmospheric pressure, the air expands by the same factor of the pressure it was under, i.e. 145 psi, accordingly ten times. This 5% air of the foam concentrate, made up 0.15% of the foam solution, expands ten-fold to 1.5% of the foam solution. We now have a proportioning rate of less than the optimum as 1.5% of the solution is air, not foam.
The pumping of foam trapped with air is more complex than the above-mentioned example due to several factors like pump speed, vacuum filling, thermal conductivity, vapor pressures. Air trapped in the foam means the system is under-dosed with a corresponding reduction in proportioning rate. Typically, we see lower than acceptable proportioning rates with higher air volume in the foam concentrate, meaning a failed foam test. Many of these issues are stated as new problems. History tells us these are the same problems foam concentrate manufacturers, equipment manufacturers and end-users were faced with, when many new formulations were released dating back to the widespread introduction of Aqueous Film Forming Foam (AFFF) in the 1970s and 1980s.
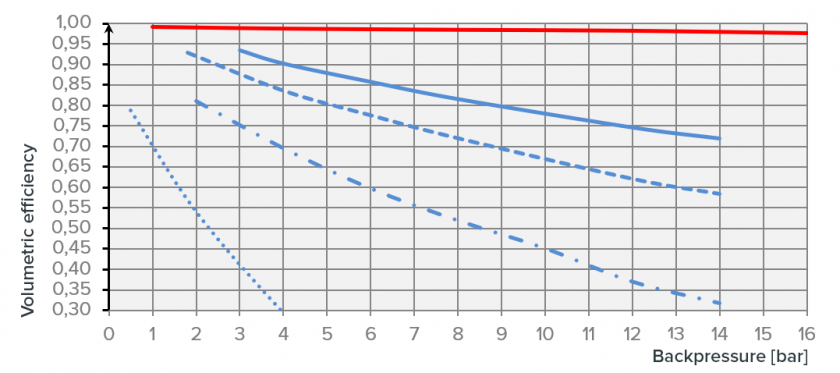
Curves show the difference between the FM-approved plunger pump technology used by FireDos in comparison to gear pumps
Equipment considerations
Different proportioning methods have different characteristics regarding the proportioning rate. In addition, sometimes their operation is affected by the foam type.
Bladder tanks and eductor proportioning
In a bladder tank, the pressure of the firewater squeezes the foam agent out of on installed bladder into the pipework and eventually to eductors upstream of the discharge device (pourer, monitor, sprinklers). This system is designed to suit a constant viscosity and flow ranges are reduced when the fluid being pumped has a higher viscosity. The pressure loss also increases due to the effort required to educt or suck the foam concentrate into the water stream. This fact applies to any system using an eductor method of proportioning, such as a jet ratio controller, balanced pressure proportioner or wide range proportioner.
Gear pumps
Balanced pressure proportioners rely on the eductor principle with a pressurized flow of foam concentrate by a gear pump requiring an external drive (electric, diesel-driven or water-driven motor). However, with varying flow rates for different fire scenarios and low viscosities, gear pumps have poor efficiencies, which results in heavily varying proportioning rates.
Water-driven variable flow & viscosity proportioners
The latest Gen III foam proportioner by FireDos was designed after many years of practical experience and using CFD techniques to optimize the pump head specifically for high viscosity foam concentrates. The traditional thinking that piston pumps are best for low viscosity fluids and gear pumps are best suitable for high viscosity fluids has been turned on its head. For accurate proportioning, high-efficiency pumps are required. Gear pumps cannot meet this requirement due to their susceptibility to different system pressures, flow ranges and varying viscosities. The flow rate range of FireDos’ water-driven variable viscosity proportioners has a ratio of 1:15 times. Means, an FD8000 at 3% proportioning rate has an FM-approved flow rate range of 138 to 2113 GPM. An equivalent gear pump might have a flow rate range of two or three times. The testament to this is the approval by the leading global fire protection authority, FM Approvals. These approvals have been designed with water motor-driven foam pump proportioners specifically for variable viscosities with standardized conditions for approval.
The new design of the proportioning pump offers many advantages, not least:
- Low-pressure loss at specific pressure conditions. For a fire protection system designer, this offers the advantage of minimizing the effect of the proportioning system on final discharge flows.
- A minimum flow threshold to achieve the proportioning rate.
- A low NPSH requirement (in comparison to traditional off-the-shelf piston pumps).
The FM testing also includes many worst-case scenarios to simulate real-life applications, such as:
- Multiple test points through the entire working range.
- Multiple test points for highly viscous fluids at different viscosity data, not only one point of the dynamic viscosity curve.
- Overload tests for pressure, flow, and dry running.
- Material compatibility/resistance tests, especially in saline environments.
Testing the proportioning rate
As firefighting foam concentrate becomes more complex, especially with SFFF, the cost rises. NFPA and FM highly recommend annual foam proportioning rate testing. FireDos achieves this by measuring the flow rate of the foam concentrate returned to the foam storage tank and the extinguishing water flow at the water motor to precisely calculate the proportioning rate. This method does work without admixing foam concentrate to the extinguishing water.
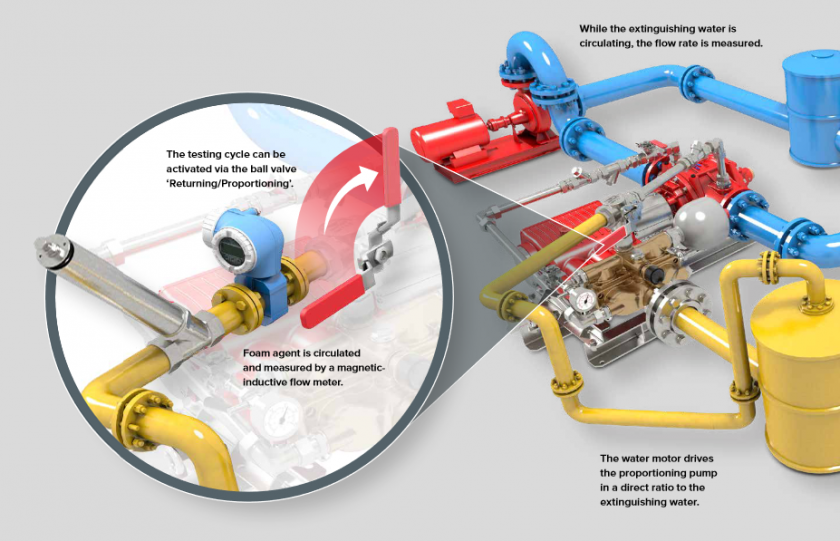
Testing the proportioning rate
Remote monitoring
Monitoring fire protection systems in testing and readiness mode provides instant feedback without needing many remote and semi-skilled or qualified personnel. This system can be operated on-site with instructions provided remotely, providing instant feedback and the creation of electronically created schedule maintenance logs. In addition, various parameters such as flow rate, proportioning rate, oil fill level and temperature are captured, so that the proportioning system is always ready for use.
A natural development of remote measurement is the ability to perform an unmanned test. As FireDos proportioners need no external energy, adding actuators to the water motor doesn’t require the start-up of any additional equipment, such as the fire pumps. Additional actuators are added to the three-way ball valve for proportioning/return. All information collected can be managed and viewed from a remote terminal or signals integrated into the end-users computerized maintenance management system.
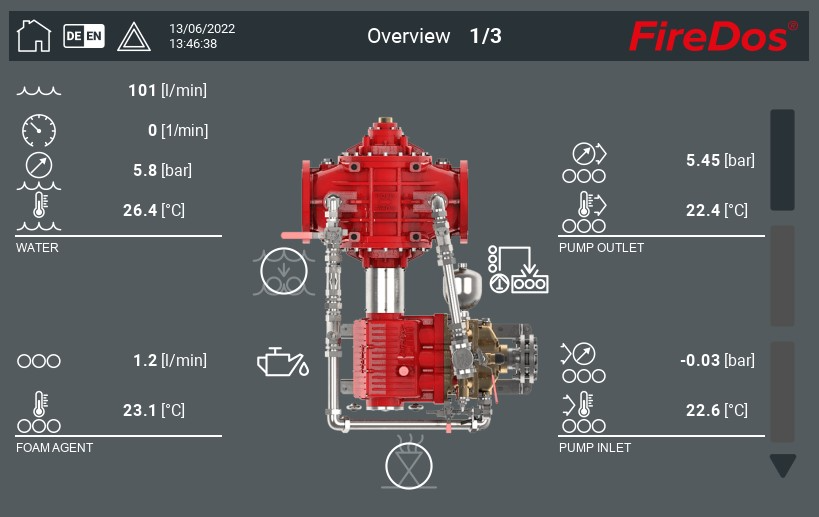
An ideal system
As fire protection systems are often legally required, the costs are considered an expense. A system with very few system components means that the investment costs within an overall fire protection system are less than many systems where redundancy must be planned (electric motor-driven foam pumps, plus additional backup diesel engines). The annual cost of foam testing is one of the highest operating costs of a foam suppression system. Accordingly, the ability of a proportioning system to test the proportioning rate without discharging any foam concentrate means it will typically pay for itself within two years compared to a lower-cost system that requires foam to be dispensed.
What does this mean in practice?
When designing and specifying state-of-the-art foam suppression systems in the future, the focus should be on the requirements of maximum precision and flexibility of the proportioning system for any type of foam concentrate, especially those with very high viscosity.
The independently type-tested and FM approved FireDos Gen III proportioners meet these requirements and have proven their outstanding performance already in hundreds of applications.
This might also be of interest for you:
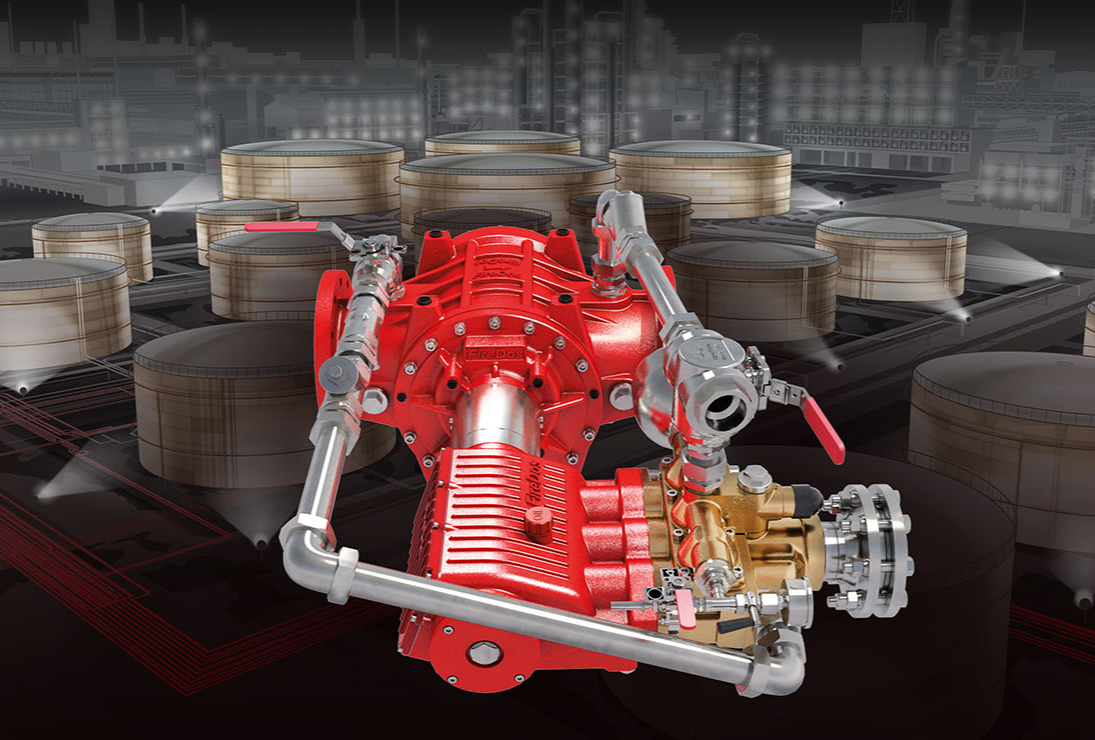
Stationary Foam Proportioners
Inrease performance, save costs: Learn more about the advantages.
View more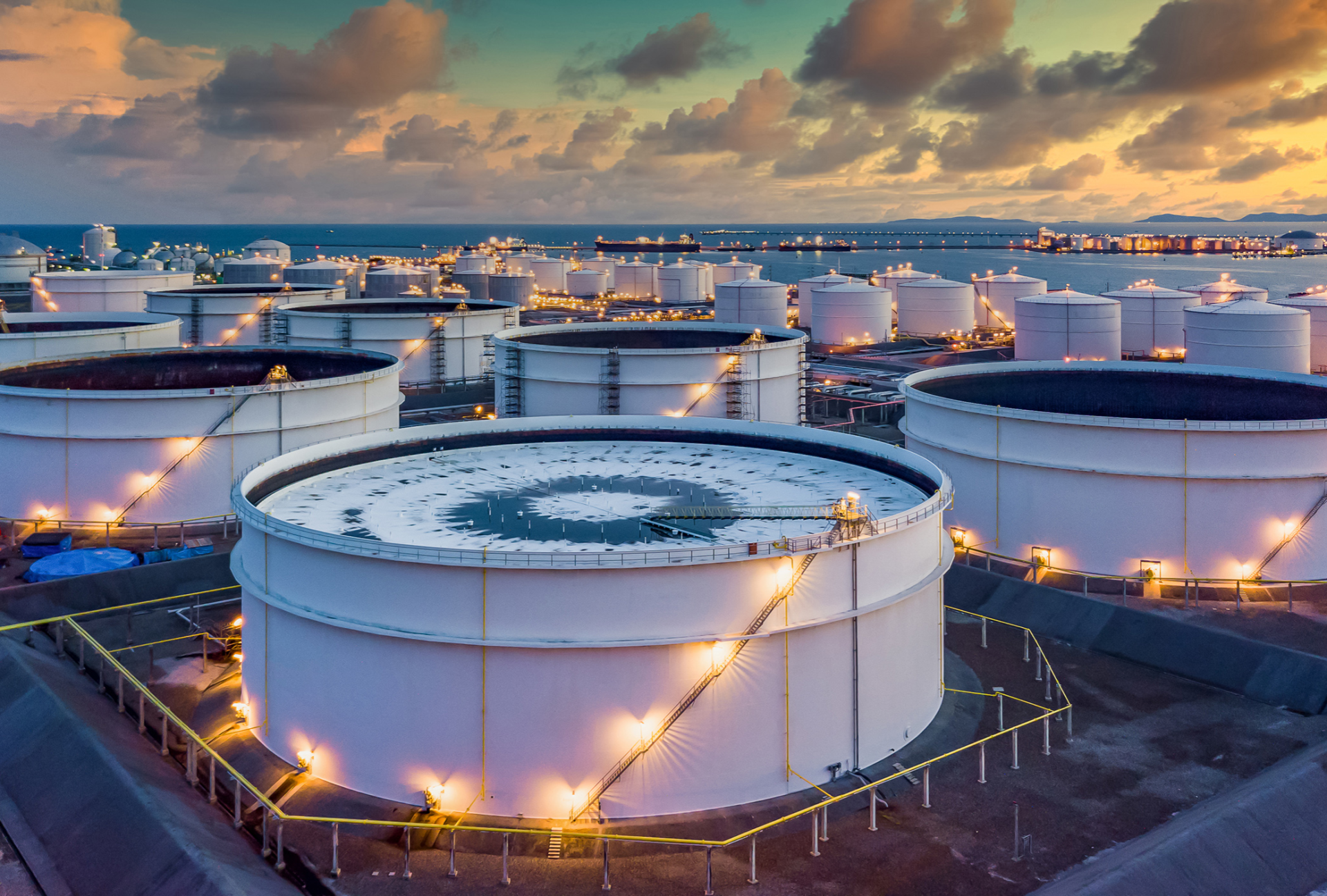
Our solutions for the Oil & Gas industry
Learn how to reduce risks through versatile fire protection systems.
View more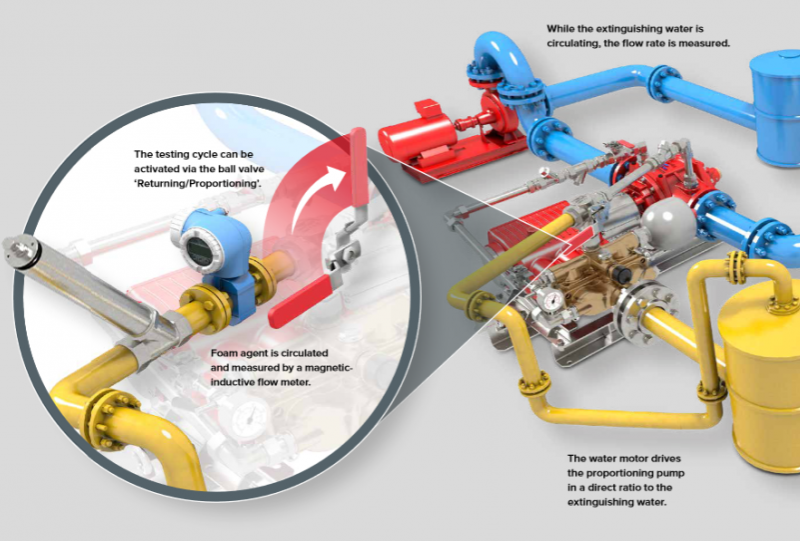
FAQs on Proportioning Rate Testing
Here we answer the most frequently asked questions about testing.
View more